Welcome to ned Productions (non-commercial personal website, for commercial company see ned Productions Limited). Please choose an item you are interested in on the left hand side, or continue down for Niall’s virtual diary.
Niall’s virtual diary:
Started all the way back in 1998 when there was no word “blog” yet, hence “virtual diary”.
Original content has undergone multiple conversions Microsoft FrontPage => Microsoft Expression Web, legacy HTML tag soup => XHTML, XHTML => Markdown, and with a ‘various codepages’ => UTF-8 conversion for good measure. Some content, especially the older stuff, may not have entirely survived intact, especially in terms of broken links or images.
- A biography of me is here if you want to get a quick overview of who I am
- An archive of prior virtual diary entries are available here
- For a deep, meaningful moment, watch this dialogue (needs a video player), or for something which plays with your perception, check out this picture. Try moving your eyes around - are those circles rotating???
Latest entries: 
The problem
Almost exactly three – yes, three – years ago I wrote here about my then recent purchase of the Dahua HFW5849T1-ASE-LED IP security camera. I was very impressed – for a few hundred euro, you can now get a 4k camera which can see in full colour in a level of dark humans can’t see in. I raised two of those cameras plus a 180 degree camera on the site shortly after getting the solar panels and fibre internet installed, which is an amazing two years ago now. Those cameras have been watching over the site ever since, alerting my phone if anybody strays onto the property using their basic on-camera AI. Each camera has a sdcard, and it continually records with about three and a half days of video history. The total power consumption for the site is 78 watts, much of which goes on those cameras (I know the 54v DC power supply draws about 50 watts, but that also goes on the PoE networking equipment and the fibre broadband).
This low power draw means I get continuous operation even with the Irish weather for ten months per year, with maybe 67-75% service during Dec-Jan depending on length of run of short overcast days. For the power budget, I cannot complain. However, if I did have more power budget:
The AI on the cameras runs on (at best) an internal resolution of about 720 x 400 by my best guess. This works fine when objects get within maybe twenty-five metres of the camera, but anything further out won’t trigger as there just isn’t enough resolution.
The AI on the cameras isn’t bad for what it is, but it also likes to think all black animals are cars. Black cats, black birds, anything black triggers it. This is annoying at 4am.
The 3.5 days of storage time is a touch limiting. You really want several weeks as a minimum.
Reusing decade old hardware
As I am me, I have a whole bunch of old to ancient spare computer parts lying around, so around this time last year I put together the least old of those old parts to see if they had any chance at all of running Blue Iris, which is a long standing reasonably priced software solution to IP security camera control and analysis. As it is a Windows program, I needed to run a dedicated Windows box in any case, but I didn’t really want to spend much money on this until after the house was raised. The base hardware specs of this ancient kit:
- Intel Pentium G3258 which was an ultra low budget dual core Haswell part able to reach 3.2 Ghz. Haswell is a 2013 era design, but it was the last truly improved new CPU architecture from Intel i.e. it doesn’t suck even today. One thing to note is that the G3258 as an ultra budget chip has AVX artificially disabled. This causes some AI software to barf at you, but a lot of software will work with just SSE surprisingly enough.
- 16Gb of dual channel DDR3-1333 RAM giving ~20 Gb/sec of memory bandwidth.
- ASRock H97M-ITX motherboard (the original use for this PC when new was within a 12v powered mini-ITX case).
- Sandisk SSD Plus 240 Gb SATA SSD from about year 2015. I remember picking it up super extra cheap in an Amazon sale and I didn’t have high hopes for its longevity, but it ended up proving me wrong.
I tested this last summer leaving it run for several months, and found that if I reduced the resolution from the cameras sufficiently, Blue Iris did work sufficiently okay that I felt confident in investing money into more of this solution. As the daylight hours began to shrink, I removed this additional power load and then, to be honest, it kinda got backburnered for a while.
Two things then changed:
I saw on a HackerNews post that the Chinese had started dumping their ten year old AI hardware onto Aliexpress for cheap as they cleared out parts they were retiring. Unlike previous AI acceleration hardware, the ten year old stuff (nVidia Pascal) isn’t too far from the modern hardware i.e. modern CUDA programs run just fine on Pascal, just slower. A cheap enterprise AI accelerator card would be game changing for realtime video analysis.
Thanks to recent economic uncertainty about the future, the price of high capacity enterprise hard drives cratered to firesale prices. I ended buying the only brand new part in this project – a Seagate Exos 28Tb enterprise hard drive – delivered for €400 inc VAT and delivery. Just a few months ago that drive cost nearly a grand. Madness.
I picked up an 8 Gb nVidia Tesla P4 card from Aliexpress for €125 inc VAT and delivery. It turned out to be brand new, never used, and it even came with its additional low profile bracket. This is a 2016 era card and it has 192 Gb/sec of memory bandwidth and can do about 5.7 TFLOPS in FP16 for under a 75 watt power budget. For the money, and for the power budget, this is a whole lot of AI acceleration – even brand new 2024 hardware would get about the same memory bandwidth and maybe twice the compute if constrained to a 75 watt power budget. And it would cost several times what this card did!
The nVidia Tesla P4 card – and indeed its whole generation of AI hardware which lacks tensor cores – isn’t well suited for running large language model AI (i.e. chatbots). But I ran a variety on 8b LLMs on it out of curiosity and it does about 18 tokens/sec until thermal throttling kicks in, whereupon you get about 12 tokens/sec. You could of course fit more cooling (you’ll see my ‘fan solution’ below), but ultimately this generation of GPU on its generation of CPU is going to be far slower at LLMs than even a recent CPU on its own. I’ll put this another way – my M3 Macbook Pro laptop handily beats the Tesla P4 for LLM performance and my Threadripper Pro workstation blows far past it. The latter has less memory bandwidth than my Macbook, but LLMs especially newer ones need more compute, and that is exactly what the Tesla P4 (relatively speaking) lacks.
All that said, while ten year old GPUs aren’t great for running LLMs, they absolutely rock image analysis which is the kind of task that generation of hardware was designed for. Identifying objects, tracking facially recognised people in crowds, 3D spatial reconstruction from multiple images – this generation of AI hardware absolutely aces those tasks as you will see later.
Finally, there was a little compatibility issue with the Seagate Exos drive and this ASRock motherboard – the motherboard doesn’t wait long enough for the hard drive to respond, and so on boot it sometimes doesn’t find the drive. I trial and errored BIOS options to slow down the boot enough that it now finds the drive 95% of the time, and if it doesn’t find it then a soft reboot fixes the issue as it avoids the drive doing a cold start. Just something to be borne in mind when pairing really new hard drives with ten year old motherboards.
The build
This is the oldest PC case I still have. It is from around 2008 I believe. It was once the TV PC for myself and Megan back a very long time ago – myself and Johanna had a TV PC in our St. Andrews house, and I think when we left I gave it away as I wanted to replace it with modern hardware, and this case was what enclosed that modern hardware (I distinctly remember with grimace the first motherboard in that new TV PC, it was a Gigabyte branded model with AMD CPU and it cost me enormous amounts of time due to quirks and I ended up junking it for an ASRock motherboard and Intel CPU out of frustration). The case, and especially its power supply which got extracted and used for other things, carried on.
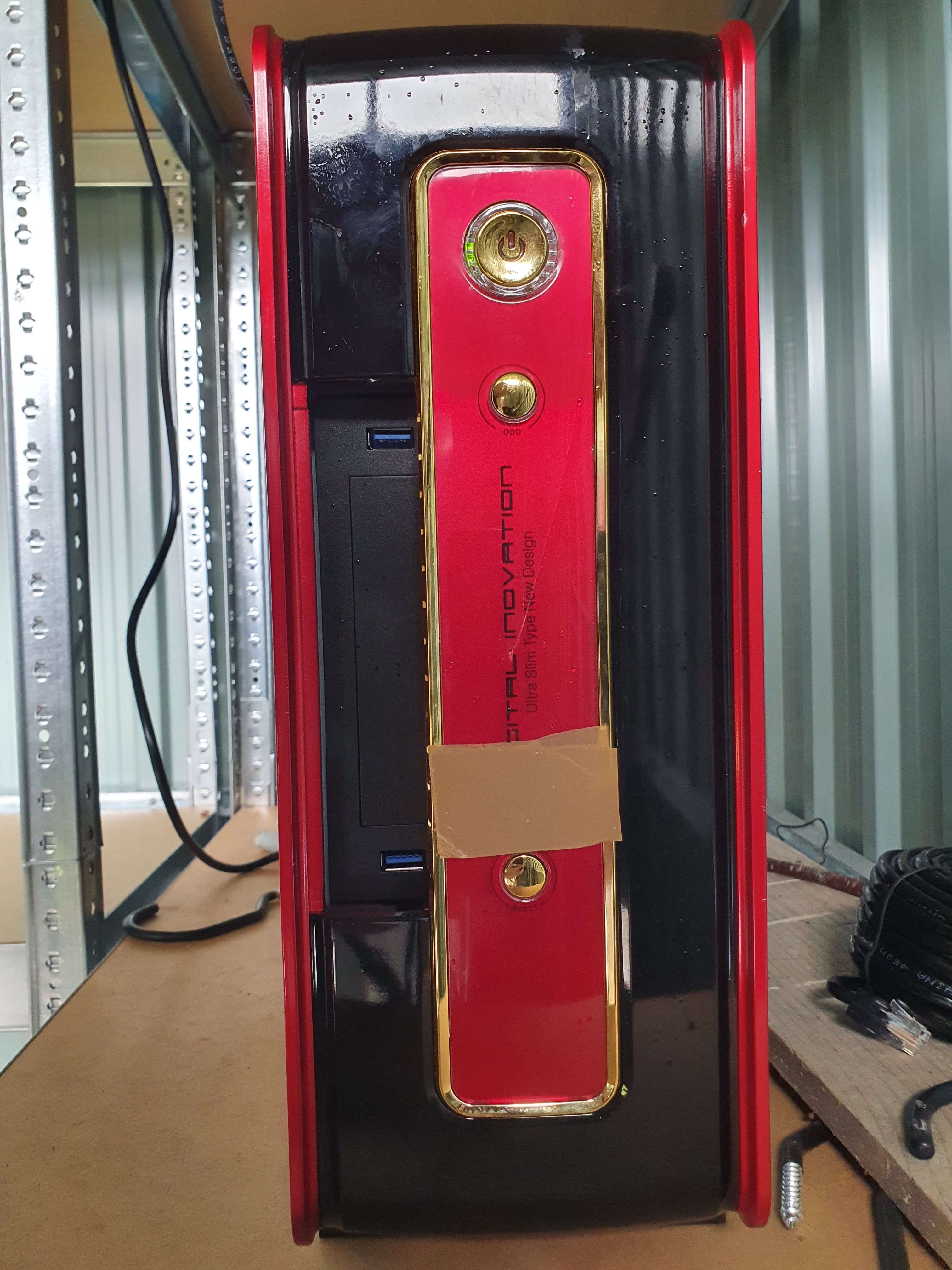
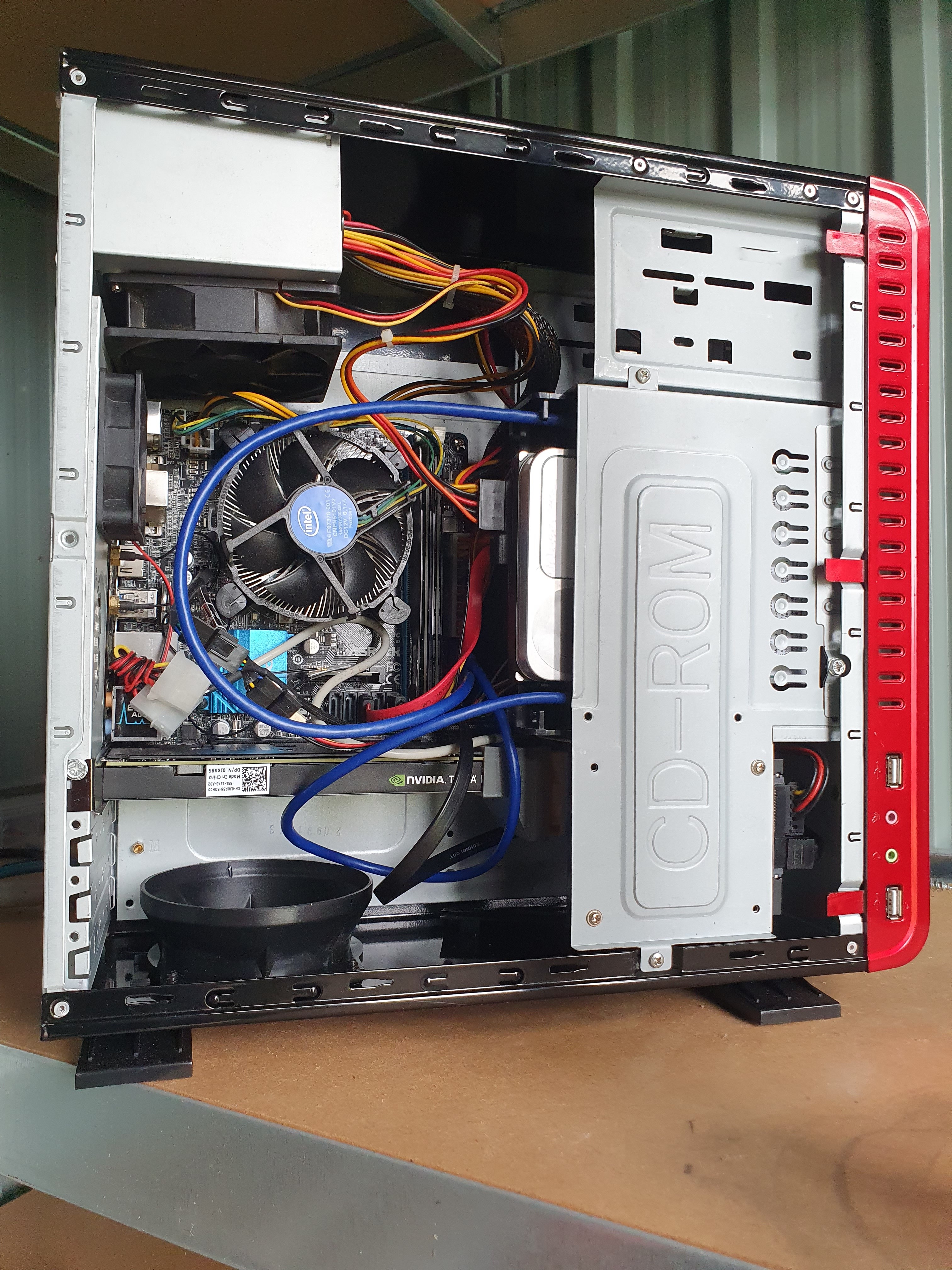
In Canada, we bought Android TV pucks just before we came back to Ireland having not used a TV PC in Canada, so this case has certainly not been in use since 2011 or so. I have been keen to put it back into use as it is one of my most favourite cases – partially because it is especially well designed, it was ludicrously cheap and even came with a power supply for the money. But I really like how tacky and garish it is. It was the perfect looking TV PC with its piano shiny black plastic with red and gold plastic. In case you’re wondering why there is tape on the front, it’s because the hard drive light is so ultra bright it’s very annoying. So we taped it over with two layers to dull down the brightness. You might notice that with this coming back into use now I took the opportunity to fit a USB3 5.25” adapter, as the motherboard is new enough to supply USB3 and I might want to copy video or something large one day. The 5.25” insert cost something like €13, it seemed a wise upgrade for this case as absolutely nobody uses a CD-ROM drive anymore, and as you may notice it can also house a 3.5” hard drive which is exactly where I mounted the Exos hard drive (there are two dedicated 3.5” bays above, but they are horizontally mounted and I wanted this drive vertically mounted as it gets rather warm – see below).
The mini-ITX motherboard has only one PCIe slot and it’s far too small for the case. But no matter – this case has enough space to fit my 3D printed fan adapter, which is my custom solution to how to cool the AI accelerator card, because enterprise cards don’t cool themselves like consumer cards, they expect cooling to be supplied to them:
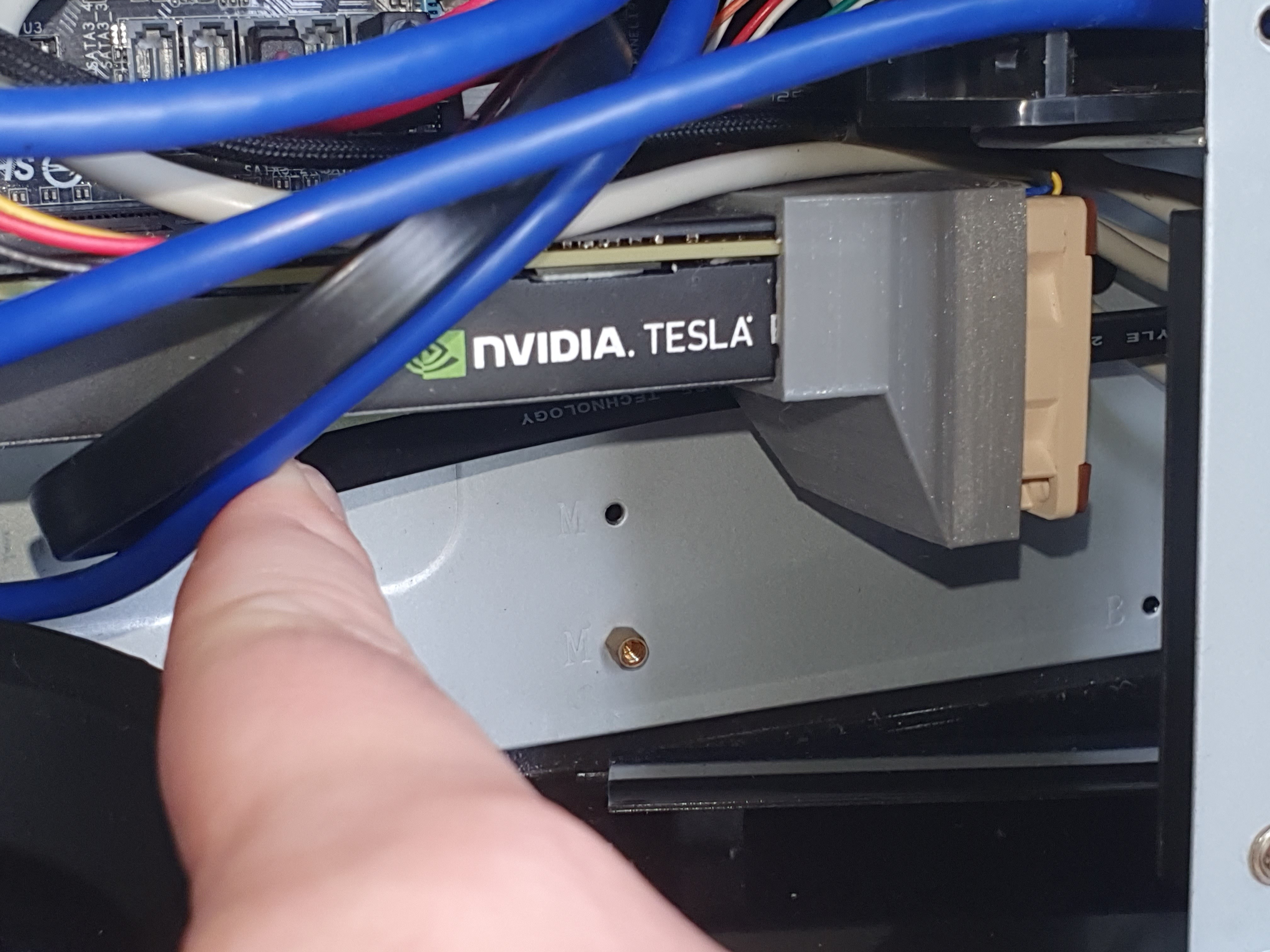
I got the design for the adapter off the internet, but I had to do a fair bit of customisation to get it to fit into the smaller original case I had in mind for this project. But eventually it was just easier to break out this much too large case, and then not sweat trying to get everything to find inside a small space. Had I bitten the bullet sooner, I could have saved myself several days of my free time … but no matter, it’s all built and working now.
At the end is a Noctua PWM fan so it doesn’t blast at full speed all the time. I chose a speed where it isn’t loud enough to be annoying, which isn’t fast enough to run LLMs without thermal throttling, but it is plenty fast enough to analyse video as we shall see.
Finally, I put in a watt meter to aid tracking power consumption of this specific PC:
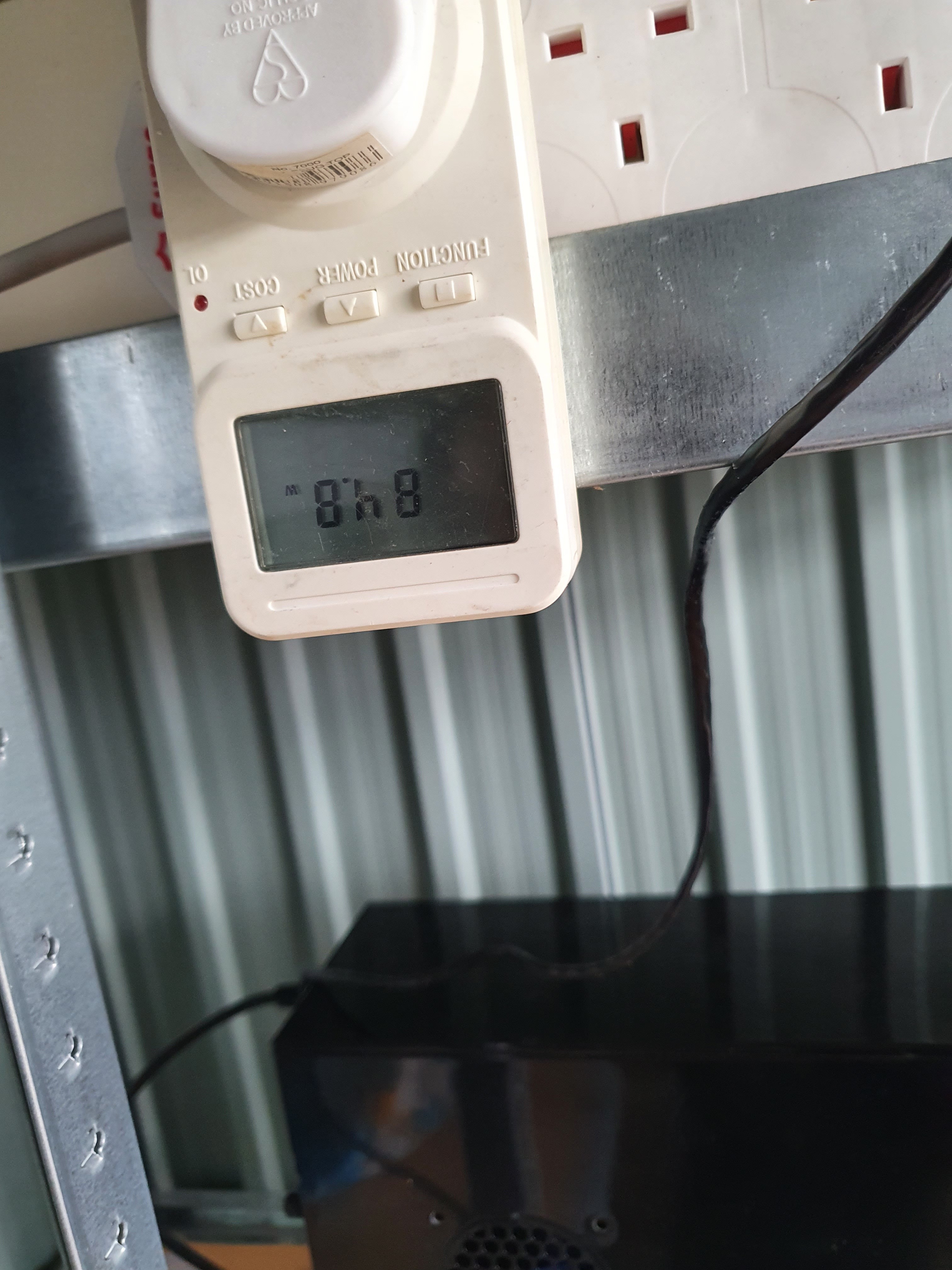
That says 84.8 watts incidentally. I think the CPU + motherboard probably consumes about 30 watts and the AI accelerator about 48 watts when it’s in use. With the fan speed I choose, the hottest part of the AI accelerator sits at about 60 C, which seems fine to me.
From the perspective of the inverter, the whole site now uses 158 watts, which if it used 78 watts before, means that this AI PC takes 80 watts on average over time. That, as with last year, will limit how long I can leave this box running with the current number of solar panels – once the days begin to shorten, I’ll have to remove it once again.
(In case you’re wondering how the maths works there, the reason more load uses proportionately less power is because conversion efficiency is lousy at low loads, so as the load rises you get less of a load increase that you would expect)
Blue Iris
Blue Iris has a Windows based UI, but also a convenient web based UI so you don’t need to remote desktop in:
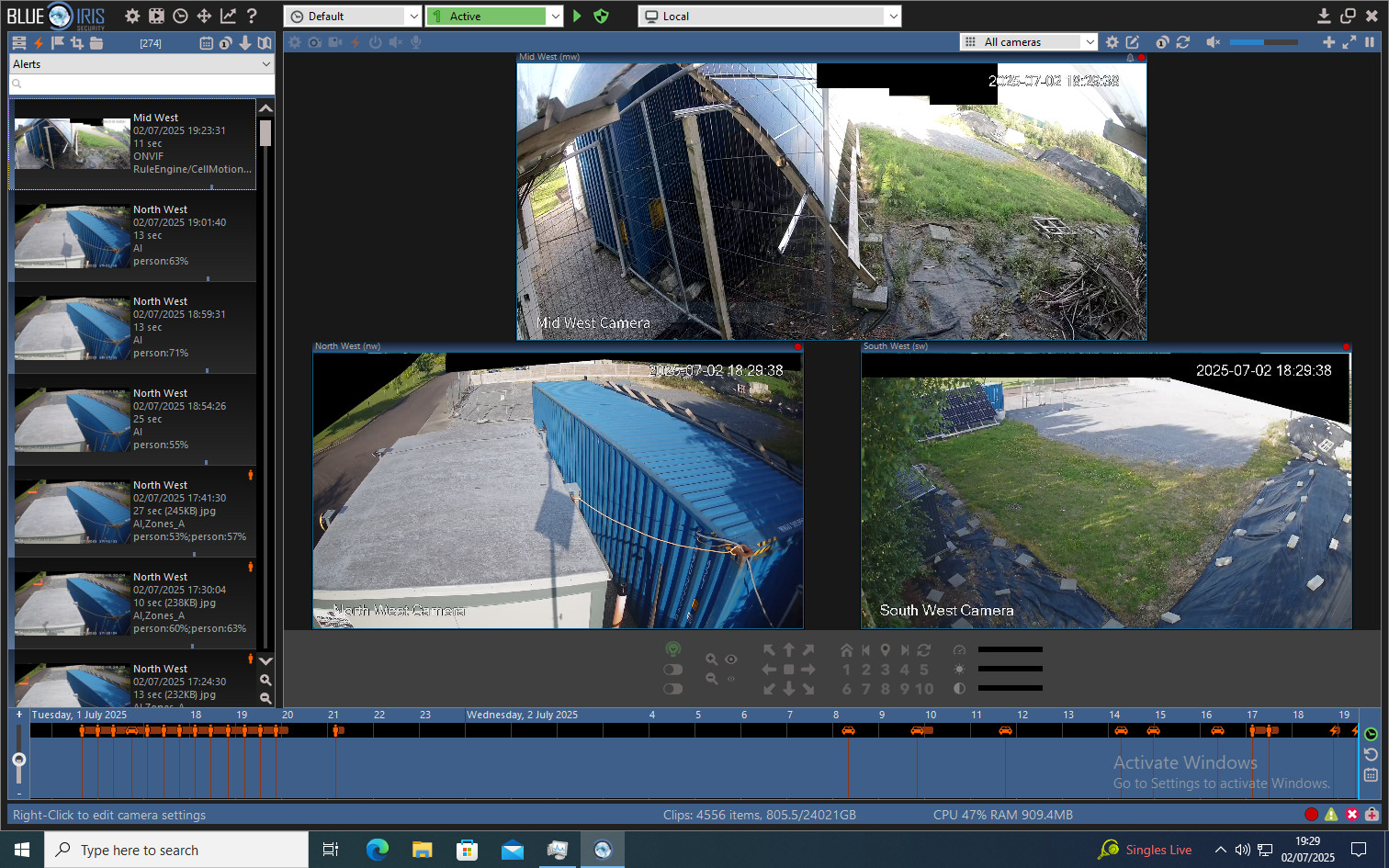
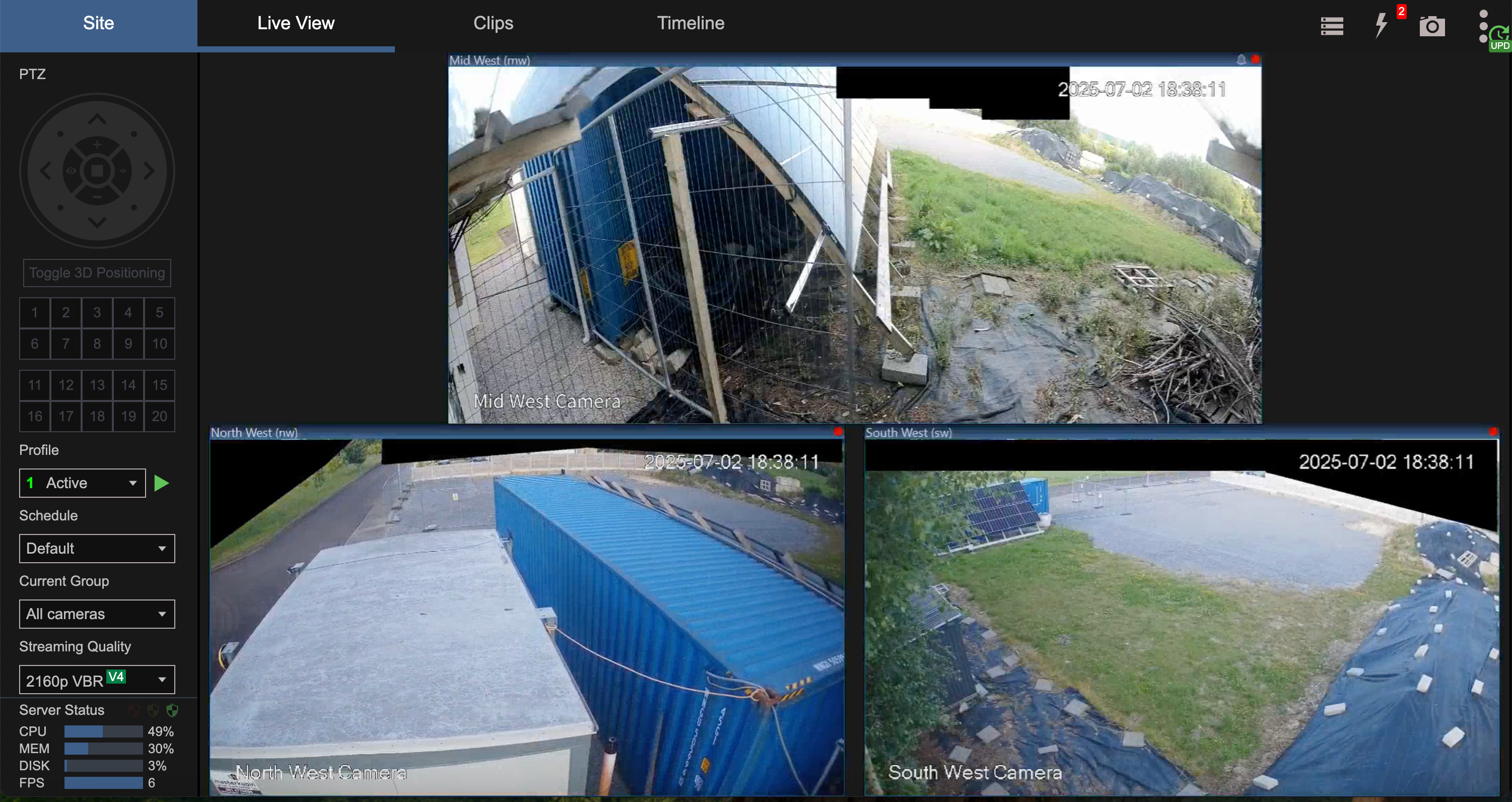
Blue Iris is extremely configurable, and it has taken me several days of twiddling before I became happy with the results. Unfortunately, Haswell era CPUs can only decode in hardware h.264 video up to 1080p. After that, it’s all software decoding. Hence three 4k resolution h.265 feeds @ 7 fps causes the CPU to peg to 100% and analysis begins to fall behind. The GPU barely breaks a sweat with 4k images, analysing each in about 120 milliseconds, and runs just above its lowest power state above idle at about 48 watts (absolutely idle is about 7 watts, incidentally, but as soon as the card gets connected to by any software power consumption jumps to 35 watts or so).
The cameras can emit a lower resolution substream for ‘free’, and Blue Iris can be told to use that substream for the AI inferencing whilst otherwise using the 4k stream for everything else e.g. storage to disc, browsing etc. Given that the Haswell CPU can’t hardware decode better than 1080p h.264, I chose exactly that for the substreams and three streams of that uses about 26% of CPU. Unusually (see below), I send them immediately to the GPU and do as little CPU processing as possible. The nVidia Tesla P4 takes about 45 milliseconds to process a 1080p image, and Blue Iris asks it to do so every second per camera. Therefore if this PC were newer hardware, this card could happily analyse twenty 1080p cameras which is good to hear, as we shall be eventually fitting eight external cameras and four internal cameras. If it could decode h.265 in hardware, maybe even eight 4k streams could be doable.
In Blue Iris terms, the current three camera setup runs at 34.5 MP/s which simply adds the bandwidths of all the cameras together. That would imply a maximum of ~150 MP/s if maxed out. I read online in forums that this old hardware should max out at around 800 MP/s albeit with AI disabled, however this CPU doesn’t have AVX and it has especially small CPU caches. Also, surely sending everything to AI immediately is expensive as it implies many more memory copies – plus I note that the AI backend is written in Python, and it eats 6% of CPU just by intermediating between the CUDA on the GPU and the main Blue Iris program.
You can, of course, tell Blue Iris to only invoke the AI if something in the picture changes. However, two of the cameras are on poles and the wind makes them wobble, so the motion detection is always being activated which means the AI is always getting called anyway. Turning off the motion detection prefilter therefore reduces overall CPU.
Storage
Blue Iris appears to write to the disc at about 0.9 Mb/sec per 4k h.265 stream. For a 28 Tb drive, of which 24 Tb is probably available for writing, that is 75 Gb/day/camera which means one camera will fill that drive in 325 days, two cameras in 162 days etc. It should take 3.5 months for the current three cameras to fill that drive, but about four weeks for twelve cameras. This is exactly why I splurged now for precisely a 28 Tb hard drive – four weeks of recordings I reckon is exactly what I’m looking for, and the first commercial release of HAMR technology hard drives is probably going to have been overengineered for durability. I guess I’ll find out.
HAMR drives generate a lot of heat when writing due to the laser assisted writing – when I was soak testing it, the write only stage generally took the drive up to a toasty 65 - 70 C whereas the read only stage kept the drive at 28 - 32 C or so. I didn’t have forced air on it, but the drive was open to the air. At 0.9 Mb/sec write speeds and in a case with at least some forced airflow, and the drive mounted vertically to aid heat being driven off of it, the drive sits at 43 C or so – I guess that laser remains turned on for long enough even at low rates of writing to generate a fair bit of heat. Heat, of course, equals additional power consumption and it is unfortunate that for my future house we shall be adding so much additional waste heat. Non-HAMR drives might only be +5 C for sustained writing, but non-HAMR capacities topped out at 18 Tb for Seagate so I guess the increased write power consumption is now here to stay.
How good is the AI?
The AI is Codeproject.AI which lets you configure which backend you prefer. After much testing, I settled on YOLOv8 though with a custom IP camera detection model loaded, as the default one generates far too many false positives e.g. finding that concrete blocks are trucks etc.
To date, with the custom model, I am impressed! It detects people at the very furthest extent the camera can see where in 1080p they are only maybe a dozen pixels high. It detects vans and cars and people which are obscured behind the cabin or shipping container. As a result, it triggers far more frequently than the on-camera AI does. But in the last few days of testing it, to date it hasn’t had any false positives except during sunrise (false negatives are, by definition, considerably harder for me to notice).
The sunrise false positives are for the middle camera only, and I think they’re due to how the light makes the complicated view look to the camera. I’m sure it’s fixable with a bit of tweaking the settings.
How do you get notified?
The camera built-in AI has an integration via its manufacturer’s Android app and a server somewhere in China. Blue Iris does also have an Android app and a cloud push server for an annual subscription, but internet feedback reckons it isn’t much good. Instead, they think wiring it into Pushover the best course of action, and there is a ‘quick start’ tutorial at https://ipcamtalk.com/threads/send-pushover-notifications-with-pictures-and-hyperlinks.58819/ which is nearly cut-and-paste easy.
In next to no time, the Pushover Android app was pinging me with a high resolution photo anytime absolutely anything at all involving a human or a vehicle occurs. I can’t complain about the accuracy nor push notification latency – indeed, I’m surprised how well it does given the downsampled 1080p input.
What’s next for this project?
Down the line, I will want to add facial recognition so the thing doesn’t go mad with alerts every time I or my family are on the site. Also, I’d like to add 3D spatial reconstruction – this is where some CUDA code takes several camera images of a scene from known vantage points, and from that reconstructs the 3D spatial location of objects. For this to work, you ideally need three cameras and no less than two cameras pointing at the same place from very different locations which I don’t currently have, so there isn’t much point in setting that up right now. Down the line however, I have deliberately designed the house camera layout so images overlap and the AI can reconstruct locations.
The reason we want the AI to know where people are is principally so lighting can be dynamically adjusted upwards and downwards based on whether humans are near a thing. So, ideally speaking, the outdoor lighting would all normally be very dim saving power and not disturbing nature. If a human – but not an animal – is close to a particular wall, the AI would brighten just that portion of the outdoor lighting. This wouldn’t just save on power, I think it would have an excellent burglar deterrence effect too because clearly something is aware of your presence.
You may remember that I originally planned to use Time of Flight sensors or Infrared sensors for this. But they’re a whole load more wiring work, and need a whole load more ESP32s to be placed around all of which then need more power, more ethernet wiring etc. As security cameras were going to be installed in any case, if they could be used to avoid all those sensors, that would be a big win. The concern was what the power consumption hit would be, and now that question has been answered.
Anyway, all that is well down the line, and I now have proven that a low power AI accelerator will do the job very nicely. So that’s another todo item ticked off for now, and another project which can be put into hibernation until the house gets built.
What’s next for this summer?
In terms of what’s next for my remaining summer, as you have probably noticed I have been making great progress at advancing my many projects and writing up my notes on them here. I have three projects awaiting testing and writeup here remaining:
- Differential pressure sensor testing.
- Thermally broken kitchen extractor testing.
- Radar human presence sensor testing.
The first I’ve mentioned here several times before. The second is to see if a Passive House grade of insulated kitchen extraction vent can be created – I’ll be empirically testing this using Megan’s hair dryer and a thermal camera. The third is a new type of sensor recently available on Aliexpress – unlike Time of Flight sensors which work on the basis of analysing the scattering of an infra red laser light, these sensors work on the basis of analysing the scattering of radio waves. Supposedly, they can tell you if (a) a human is present (b) if that human is standing, sitting or lying down and (c) they have a range of about five metres. If they really can tell human position accurately, they would solve my ‘bedroom problem’ because I can’t fit cameras inside bedrooms, so a sensor which can tell if somebody is in a bedroom, and whether they are sleeping or not, would be very handy.
We ended up purchasing a Fiido D11 2025 edition for Megan’s commute bike, so I’d expect a short post here on that at some point.
I’ve been and returned from my final ISO WG21 C++ standards meeting in Bulgaria, and I have cranked out four papers for the next ISO WG14 C standards meeting. So that’s all done.
The trips to Amsterdam and London have been planned and booked. This Monday I’ll even get cleared another unpleasant todo I’d been putting off, a colonscopy.
There are two things I have not made good progress upon so far:
- Losing weight (I remain at 84 kg despite substantially reducing my caloric intake and increasing frequency and duration of exercise).
- Complete the 3D services layout plan, which I ‘mysteriously’ keep finding excuses to not do because I dislike doing it so much.
I’m sure that as the low hanging more enjoyable fruit gets harvested, I’ll have ever fewer excuses to not get moving on the less enjoyable work. Here’s hoping!
There are only a few occasions that I can think of in my life where I have been singularly unsuccessful over multiple years of trying. Usually I am quite effective at anything I apply myself towards. But it turns out that I am no good at standardising C++. I still think that’s far more on the dysfunctionalities of WG21 than it is on me, but seeing the glacial progress of my house build … well, clearly there are some things where me applying myself does not yield timely results.
As mentioned a few posts ago, there has been forward progress in my house build in that the timber frame supplier (builder) has finally provided a set of design plans and those have been since signed off by my architect. So, to recount the overall timeline to date:
- 2020: We start looking for sites on which to build.
- 2021: We placed an offer on a site.
- 2022: Planning permission obtained (and final house design known).
- 2023: Chose a builder.
- Feb 2024: Lost the previous builder, had to go get a new builder and thus went back to the end of the queue.
- Aug 2024: First draft of structural engineering design based on the first draft of timber frame design.
- Nov 2024: Completed structural engineering design, began joist design.
- Mar 2025: Completed joist design, began first stage of builder’s design sign off.
- Jun 2025: First stage of builder’s design signed off. Many more stages left to go.
The reason that the builder’s design is not the architect’s design is because the timber frame, joists and the steel are both specific systems and the architect’s design is more generic, and not based around a specific supplier’s specific components. Therefore, new designs must be derived based on the architect’s design, and the architect’s design modified where necessary to match the constraints of the build technologies used. Here is the design as was signed off by the architect this month:
Builder's IFC 3D models: left is with timber, right is steel only
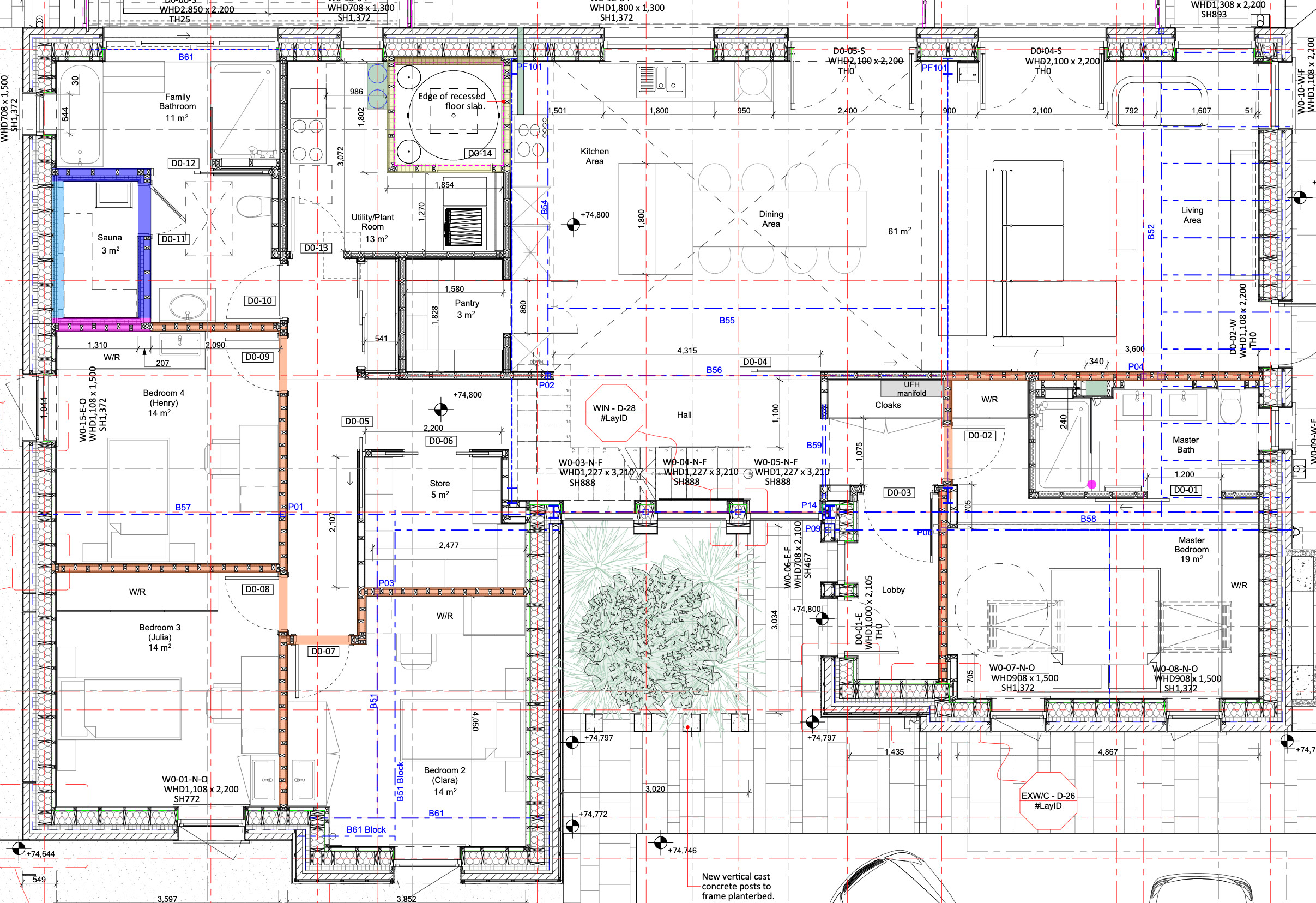
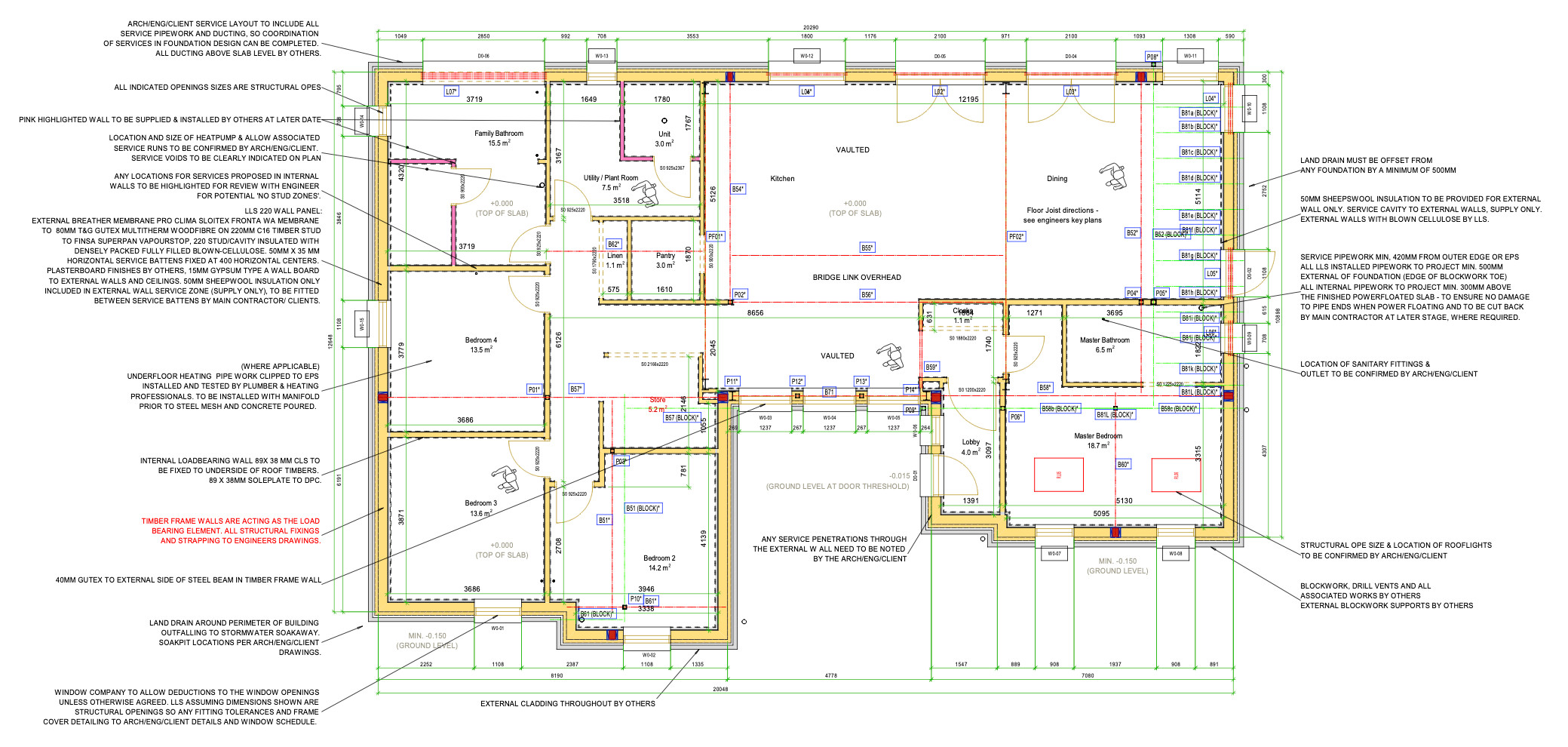
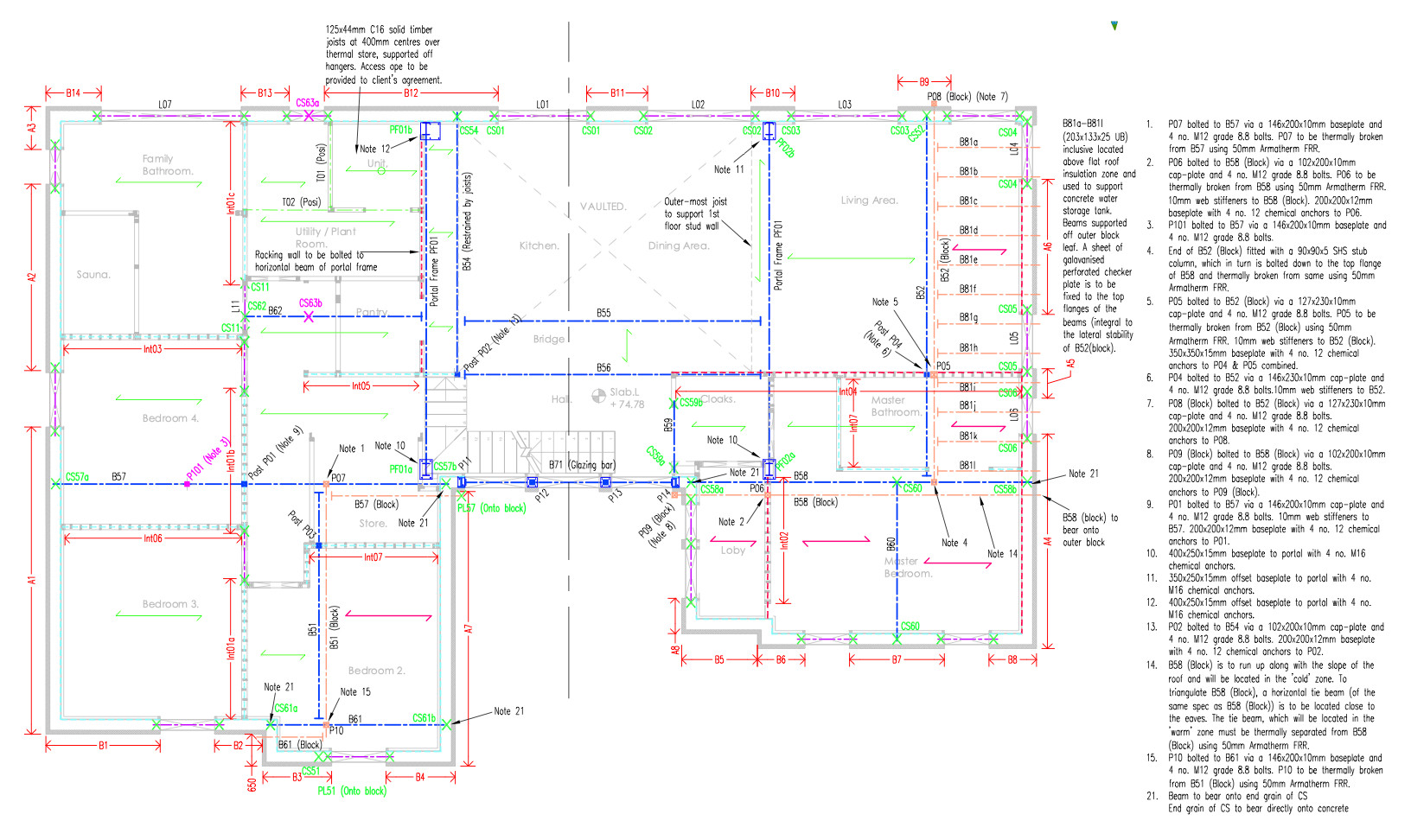
Ground floor: left is architect's design, middle is builder's design, right is structural engineer's design
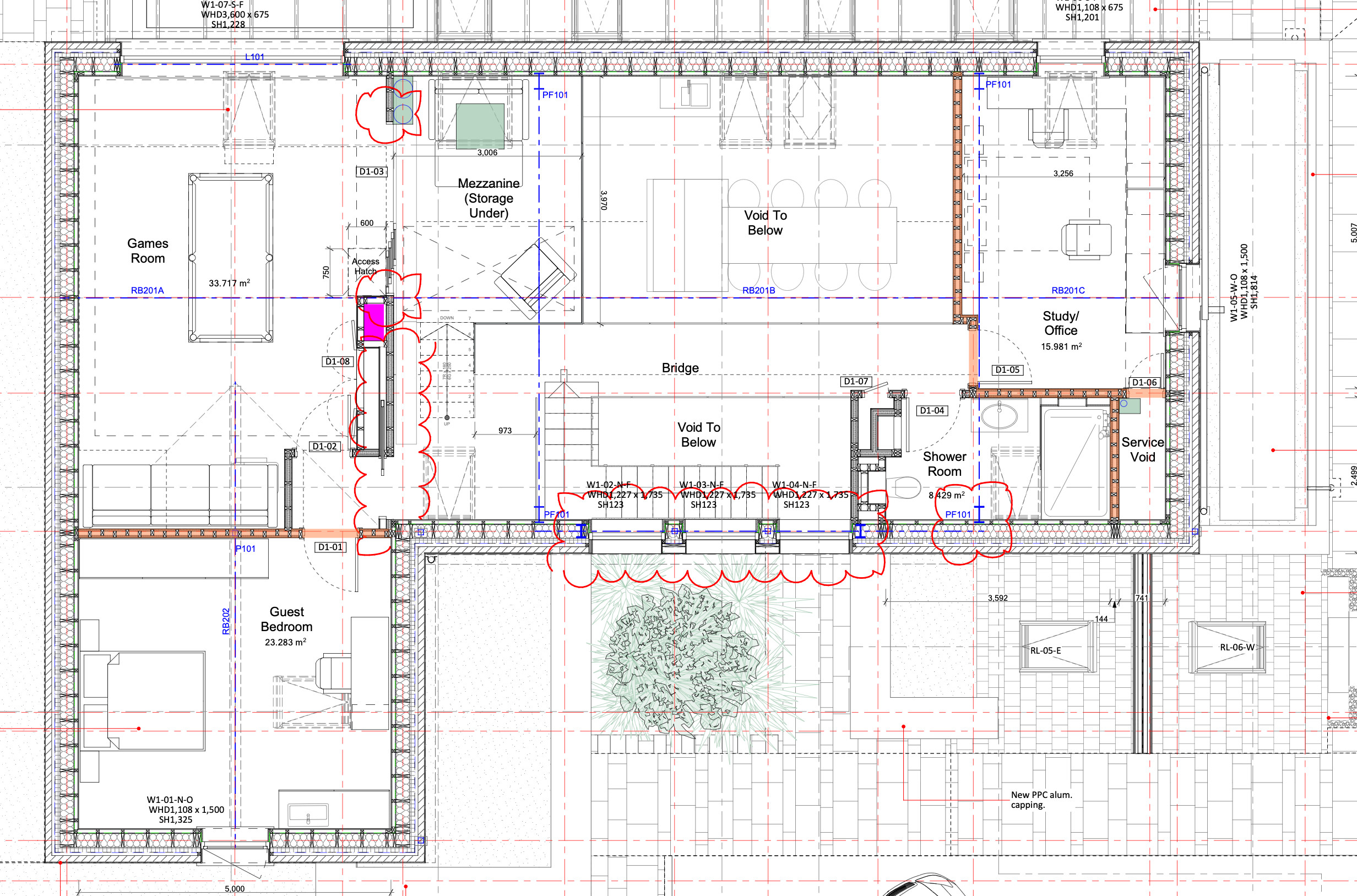
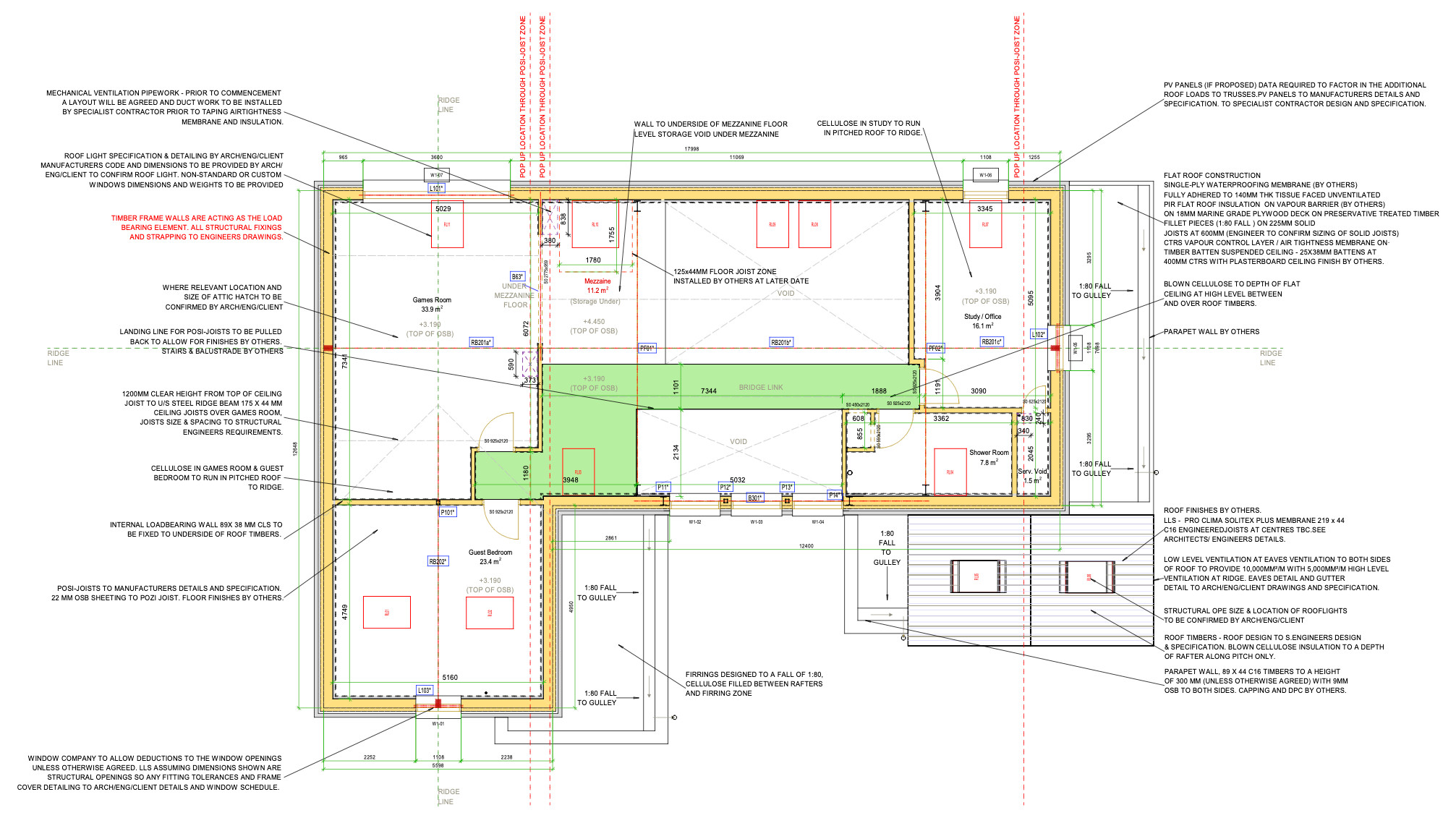
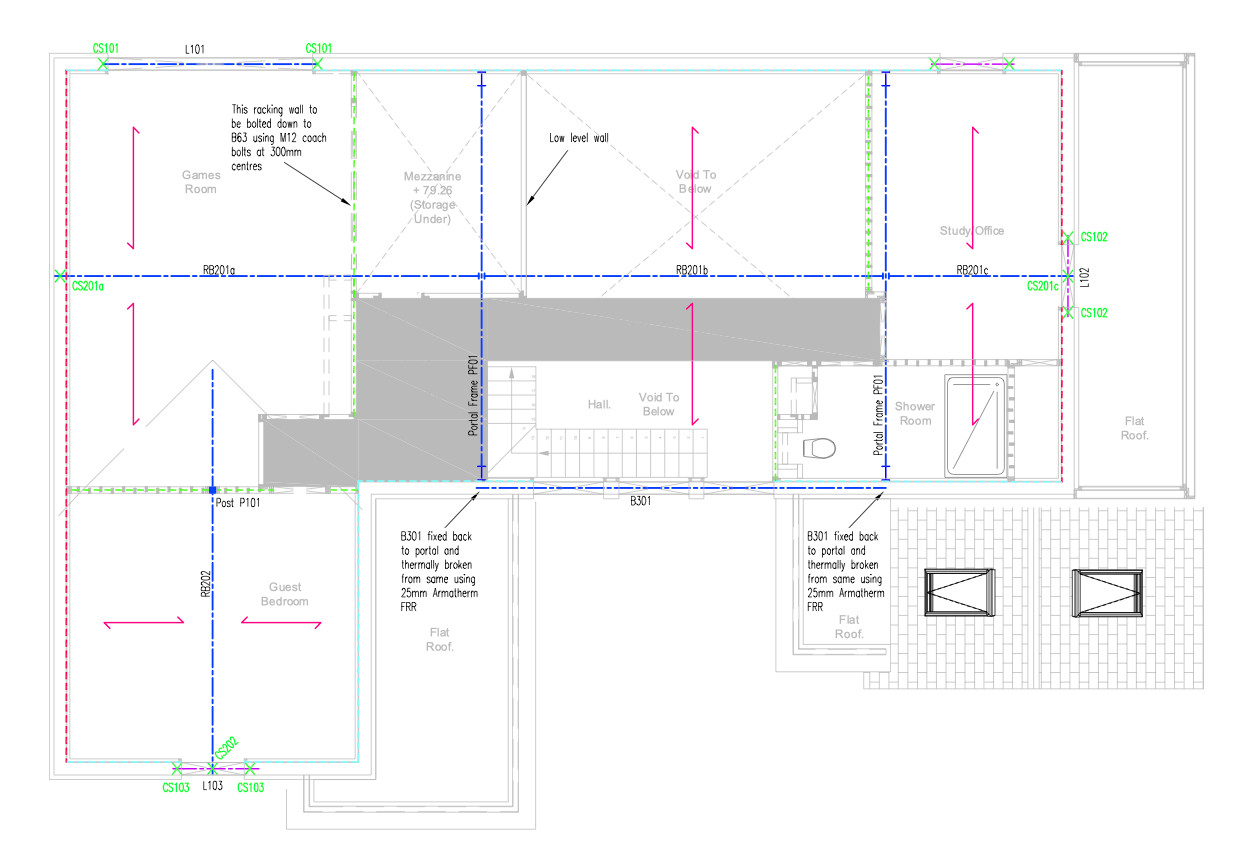
First floor: left is architect's design, middle is builder's design, right is structural engineer's design
I don’t have anything really to say about these that hasn’t been said before. Many months have passed, very little material change has happened in the designs above. It’s basically exactly the same design as it was Spring 2024.
I have no idea what the builder will want to supply and install this. Whether we build soon or don’t build soon will hang on that final quotation.
(Yes I know most people laid off go on a spending binge as a psychological coping mechanism, but I swear I’m different – I’m finally free of the Eye of Bank Sauron questioning every ‘unusual’ spend of my money that I personally worked for and earned, so yes I let loose a bunch of pent up spending on things I’ve wanted for a while)
As mentioned a few posts ago as priority item number two for my period of unemployment, I’m going to be spending a lot more time with my children this summer than they have ever had before. We have five days in Amsterdam and another five days in London together coming up. For the nine weeks of summer remaining, when the weather is good I expect to be taking them on day trips somewhere in Ireland (which is after all a tourism superpower), or somewhere local. We fortunately live in the middle of some of the best hiking country in the world, but most of it hasn’t been doable due to short legs not being able to hike far. I believe I have solved that problem and several other problems simultaneously by purchasing a cargo e-bike which can carry two children with me!
Choosing a bicycle
Henry happened to take Clara’s bike for a spin a few weeks ago, from which it became obvious to all that Clara’s bike is the right size for him and therefore Clara now needs a new bike. It’s kinda painful to admit that Clara’s new bike is probably Megan’s adult bike. My how she has grown!
Which means Megan now needs a new bike, and luckily four years have elapsed since we last bought a bike under the Irish government’s Cycle to Work scheme which at current rates allows an employer to purchase a bike for its employees up to a limit of €1,250 for a push bike, €1,500 for an electric bike, and €3,000 for a cargo bike. The employer may purchase this bike up to those limits not as a benefit in kind and without inducing tax of any kind, and therefore it comes out of pre-tax money which is 38.5% of post-tax money i.e. that €3,000 bike is equal to €1,155 in post-tax money. It is therefore one of the most efficient things a micro business in Ireland can spend money upon.
I’ll set aside how immoral taxation at a 61.5% rate is by definition to focus on ‘what can you get today for under the Irish government limits?’. Four years ago a Trek FX3 Equipped was bought, and four years before that a Trek FX2 was bought under that scheme. Both are fine bikes, and we learned that having the manufacturer equip the bike with luggage racks and stands etc was a far superior bike than aftermarket equipment and the Irish Revenue scheme doesn’t care what is bundled with the bike so long as it’s under the price limit and any additionally purchased items not in the bike order are on Revenue’s approved list of permitted additional purchases for bikes under the scheme. We could go for another Trek FX3 grade of bike and stay under the limit. Or we might try something else.
Choosing an electric bicycle
I decided to take a punt on something else: a cargo e-bike, which might complement our existing bikes none of which are going anywhere (and why buy a duplicate of what you already have?). Unfortunately cargo e-bikes which are anyway reasonably specced are far beyond €3,000 in the current Celtic Tiger frothiness. So I was constrained to direct to consumer Chinese vendors the biggest of which in Europe are ADO, Engwe and Fiido.
There are at least a dozen such direct to consumer Chinese vendors operating in Europe. And many more again under the likes of Halfords ‘own label’ marks etc. Personally speaking, I’d tend towards the Western marks (even though they’re made in China) as the quality tends to be a touch above. However, in battery and electric motors, the Chinese undoubtedly lead the world. Those BYD batteries I bought for the future house are second none in my opinion – world leading. The inverter is not quite as good as European inverters, but given it’s half the price and it’s definitely at least 80% as good, I’m sold. I suspect the same applies to e-bikes even if it does not to push bikes. Yes the non-EV bits will be inferior, but if half the price and if the EV bits are superior, that works for me.
ADO and Engwe appear to be strongest on folding e-bikes – most Deliveroo riders choose an Engwe, a few choose an ADO, and I would assume they would not if they weren’t good value for money. ADO’s bikes cost a bit more than either Engwe or Fiido, but they’re a bit better made, and usually a bit lighter through better design rather than simply throwing more metal at solving problems. In particular ADO appears to make more use of extruded aluminium, whereas the others weld their aluminium. Extruded aluminium doesn’t suffer from weak points at the welds, so you can make the frame lighter and thinner without risking fracture. Engwe and ADO can use mid mounted instead of rear mounted motors. Engwe tends to be the first to market with new technology or refinements. Fiido and then ADO tend to follow after.
All these general statements apply to the general bike offerings, and not necessary to cargo bikes, which are ones designed to carry luggage. Of the cargo e-bikes that ADO, Engwe and Fiido offer – and do bear in mind the current models have been on the market about eighteen months in total after their vendors entered the direct to European consumer business no more than five years ago – ADO’s cargo e-bike clearly was not competitive in terms of price to spec, and the rebadged own brand labels suffered from a lack of online reviews as to their quality. This left the Engwe LE20 cargo e-bike for €1,599 inc VAT delivered and the Fiido T2 Longtail (2025 edition) cargo e-bike for €1,499 inc VAT delivered. Both suffer from extensive ‘aggressive brand management’ typical of Chinese direct to European consumer businesses whereby paid shills and trolls are employed to ‘manage’ the brand identity in a way offputting to most Europeans because it is rather too forced down the throat. To be honest, they’d do better in Europe by letting the product speak for itself, and not trying so hard with the public image which makes it look like they’re trying to hide something. Still, excessive execution on the brand management side can mask actual value – nobody today would say that BYD cars aren’t competitive with any other, and that’s partially because BYD learned to be less publicly insecure about how good their stuff really is.
Having decided that a direct to consumer cargo e-bike was definitely the proposed buy, I read everything I could online about the Fiido T2 Longtail and the Engwe LE20. Most Youtube reviews on these were fairly obviously incentivised, and most Reddit and other social media and forum posts were also questionable. It really didn’t help that conventional bicycle comparison reviews refused to include cargo e-bikes from these direct to consumer vendors, so you’d have this comparison review of twelve cargo e-bikes from all the major Western brands and not a single Chinese brand in there. Luckily, with enough foot leather expended, you can eventually find individual comments and mini-reviews by people who are cycling the major Western brands AND a Engwe and/or Fiido. If after researching their account I felt they were an actual genuine true person not being paid to write what they were writing, their opinion was ranked very highly relative to others.
I mention all this to explain what comes next, and before that I ought to list specifications:
Bike | Price | Battery | Weight | Claimed torque | Brakes | Tyres | Gears | Notes |
---|---|---|---|---|---|---|---|---|
Engwe LE20 (2025 edition) | €1,349 after discounts | 922 Wh | 36.8 kg | 100 Nm mid drive | 180 mm hydraulic | 20 inch by 3 inch | 7 speed Shimano Tourney | has turn signals |
Fiido T2 Longtail (2025 edition) | €1,384 after discounts | 998 Wh | 39.5 kg | 55 Nm rear drive | 230 mm hydraulic | 20 inch by 4 inch | 7 speed Shimano Tourney | can be unlocked from EU regulations |
(the discounts from the list prices above can be had by collecting youtube review referral discounts, which obviously proves that the review is incentivised. Still, it can save you a few hundred euro)
I’ve emboldened the outstanding feature of each bike, and underlined the weakest. To be clear, both of these 2025 models have torque sensor pedals not the cadence sensor pedals typical of 2024 and earlier models in this price range. Both are EU regulations compliant in having a motor constrained to 250 watts and a maximum speed of 25 kph, which their 2024 models were not (and indeed which famously resulted in some Engwe bikes in the UK being very publicly destroyed by the government). Both have Shimano front suspension forks to soak up the crappy roads typical in Ireland and the UK.
And, despite being more expensive, heavier and having an apparently lower spec, I plumped for the Fiido. Here it is after completing assembly, and then with Julia on the back sitting in the ‘child cage’ optional accessory which also doubles as a goods carrying basket if you fit the bag fabric:
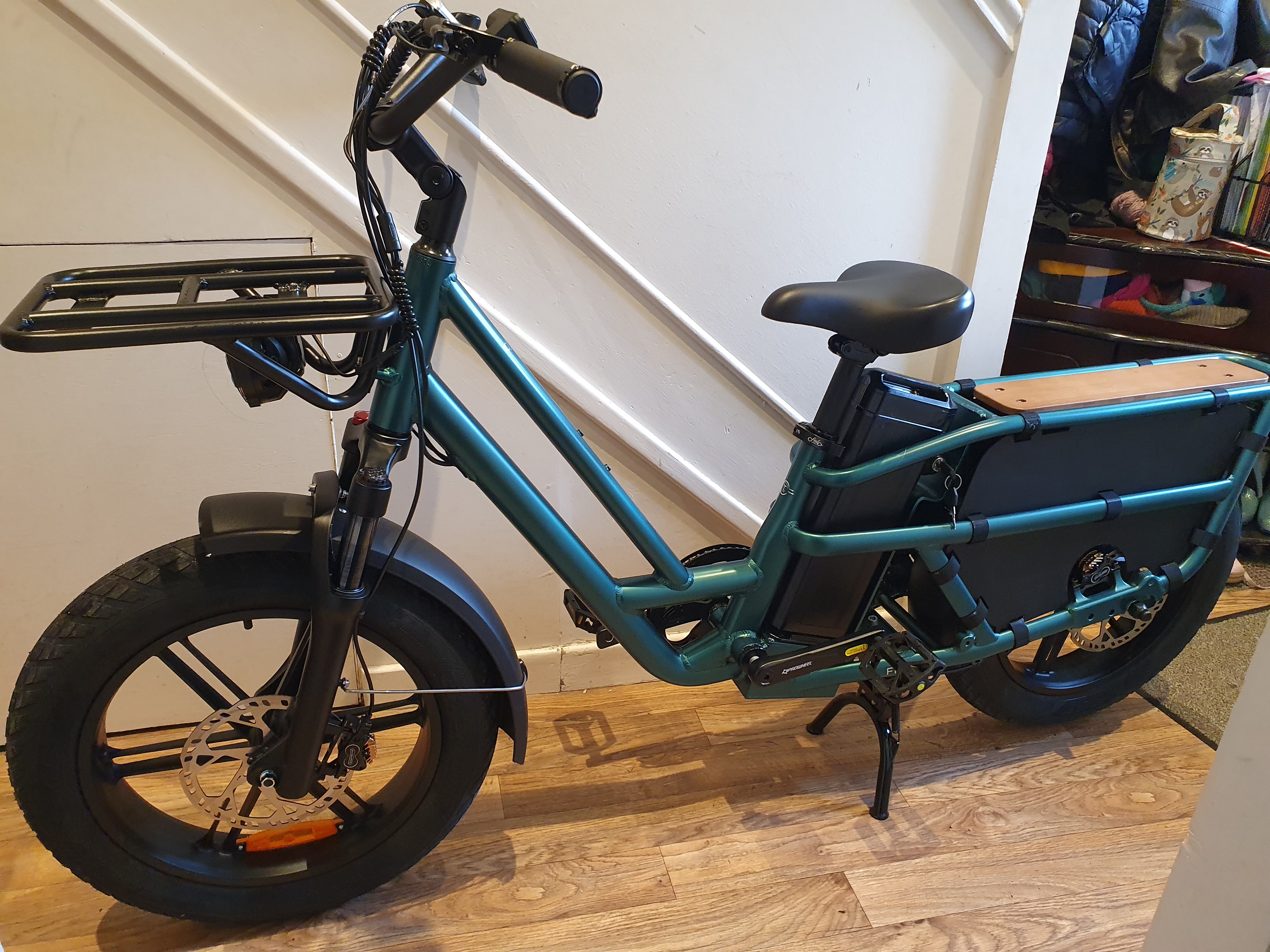
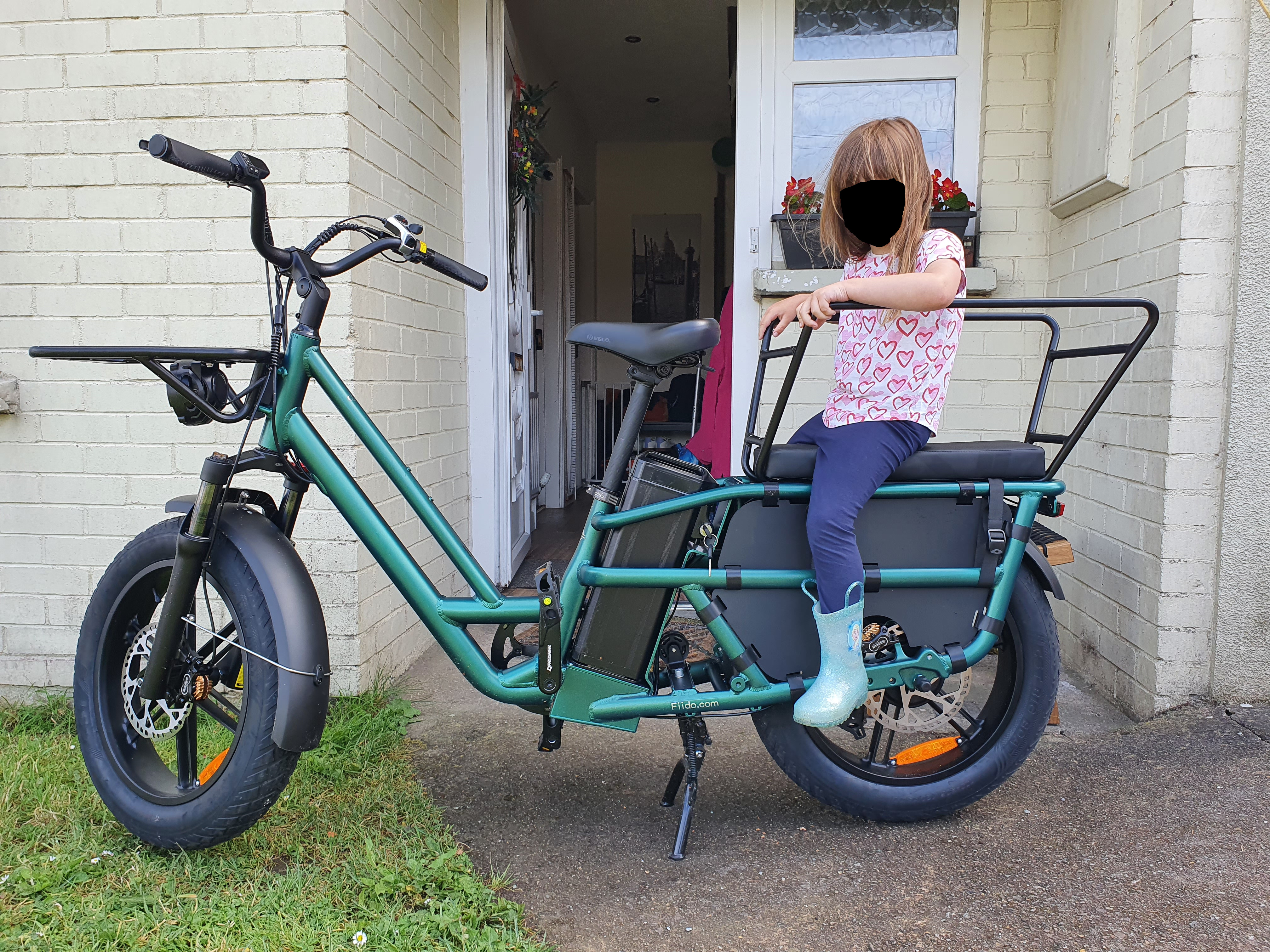
So why did I choose the Fiido T2 Longtail instead of the Engwe LE20?
To be clear, either is a great cargo e-bike in the sub €1,500 price range (and also to be clear, neither is as good as a €3,000 or especially a €4,000 cargo bike). But from very extensive cataloging of what I reckoned were likely trustworthy user feedback and reviews, the Fiido beat out the Engwe despite the clearly worse specifications.
I should caveat that claim by the reviews last year were tainted somewhat by the Engwe being then a few hundred euro more expensive, which is no longer the case now it’s cheaper. Everybody agrees the mid vs rear drive is superior, especially as the Engwe has an especially torquey motor and gears can be applied to turn that motor into any ratio of drive you want which means far less slowdowns on steep hills. The Engwe is lighter, the Engwe has turn signals which reviews of the Fiido T2 often mention is lacking. One probably ought to have chosen the Engwe given the higher spec and lower price.
However I decided to follow the evidence first: put bluntly, there were more positive reviews that I trust of the Fiido than the Engwe. Many mentioned that the Engwe’s seat was especially awful, whereas the Fiido’s seat was just bad. I became convinced after my research that if you’re going to go fat tyre, then go fat tyre all in and therefore the four inch fat tyres beat the three inch fat tyres. And, finally, the braking: everybody, absolutely everybody, agrees that the braking on the Fiido is by far and away amongst the best braking on a bike anywhere. The brakes are branded models, and they normally fit that brand and model on motorcycles. And yes you can absolutely tell that – I went from 50 kph to full stop while going down a hill in under three metres. The Fiido has phenomenal braking power between its brakes and its motorcycle style fat tyres which grip the road far better than thinner tyres. Better than my Trek bikes, which weigh maybe 18 kg versus the ~40 kg of the Fiido. The Fiido I am quite sure would stop the quickest from speed of all my bikes. And that, when I expect to have two of my children on the back of this bike, really does matter to me.
Yes I know most bicycle enthusiasts hate the fat tyres common on Chinese branded bikes. They add weight and road noise, reduce manoeuvrability and rate of turning at speed, and have more rolling resistance which means they’re harder to pedal and reduce battery range. For some reason – I assume market demand – Chinese branded bikes fit bigger batteries and more powerful motors i.e. adding even more weight whilst still keeping the fat tyres. Me personally – I’ve ridden motorcycles and mopeds before, so I’m more used to fat tyres. I know they’re better on loose stone, and far better on sand than bicycle tyres. As mentioned last paragraph, all that extra grip makes for superb braking but it also means you don’t feel unsafe at 50-60 kph like I do on my Trek bikes. I think fat tyres are just a different cycle experience, they have their pros as well as their cons. Their biggest con in my book is the harder pedalling, but for an e-bike it’s rare you actually have to push the pedals by much. Similarly, the added weight matters much less when it’s the motor pushing the bike around rather than me.
The other cause of my choosing the Fiido is that you can still disable the EU imposed power restrictions via an engineering debug menu, whereas Engwe due to the very public crushing of their bicycles on social media has completely removed that option. I’ll be very blunt here: I can personally testify that the Fiido with EU constraints removed is a very different bike to EU constraints imposed which is the default. The unshackled bike is a monster, oodles of torque and power. Is there a 15% gradient hill ahead? I’ll power up that at 20 kph with an extra child onboard. I’m currently personally a little heavy at 84 kg, so on the flat alone unshackled bike reaches about 40 - 42 kph. But even unshackled it remains shackled to a max power assist below 50 kph which is a shame because it’s never uncomfortable nor is there ever feelings of unsafety at 60 kph which I can reach going down a steep hill. I wish they’d allow unshackled power assist to 60 kph … but okay, this is a sub €1,500 e-bike, and we’re already into illegalness in the EU if you go faster than 25 kph on a public road.
Having compared EU legal vs what the bike can actually do … the EU regulations are plain dumb and stupid. If I have a licence to drive a car and I have driven the past decade without even a parking ticket never mind a speeding ticket, why should my bike which is perfectly safe at 50 kph be artificially limited to 25 kph? Why can I drive a car at 50 kph but not a bike – which is far less lethal – also at 50 kph?
There is an argument that cars shouldn’t be allowed to drive at 50 kph in urban areas either, and should be constrained to 30 kph. If drones can be constrained based on location, and so can cars, why can’t e-bikes? The app on your phone knows your location and speed limits. It could impose geolocated 30 kph or 50 kph limits same as for cars for people with valid driving licences. Then, if you’re out on rural roads, you can open it up.
I think the EU could do far better here. Absolutely insist on bikes having better braking power than cars as a start. For those who validate their driving licence with the app, I’d raise the maximum speed to 30 kph as 25 kph is just a touch too slow, and I’d make those speed restrictions geolocated same as for drones and cars.
I expect nobody able to do something about it will be reading this so it won’t matter. But it just seems a missed opportunity to me. With the range and carrying capacity a cargo e-bike has, it’s a viable alternative to a car for short runs like to a shop. We should be encouraging that, not discouraging it.
The negatives of the Fiido T2 (2025) longtail e-bike
I feel that I haven’t been fair. I’ve been all positives and I haven’t mentioned any negatives about my choice of the Fiido bike, and it wouldn’t be fair if I did not. I should point out beforehand that everything I say here refers to the 2025 edition of this bike. Later editions will probably be better, and the 2024 and earlier editions are definitely worse.
Our Trek bikes have mid-range bike gear, so their gear changing isn’t the worst but isn’t the best either. Similarly for the brakes – our FX2 in particular has the old fashioned rim-based brakes, whereas our FX3 has hydraulic disc brakes. If I am honest, I am unconvinced that the FX3 is worth 2x the cost of the FX2 which was the purchase price difference. Yes the FX3 is better in many areas, but nowhere near 2x better overall. In this, I think push bikes are like whiskey – after a certain point, 2x the cost is at best +20% better. I mention this now, because it will make sense later.
The Fiido definitely has cost reduction elements about it. It is good that they chose anything Shimano at all given how bad some of the bottom range Chinese derailleurs are. But that said the Shimano Tourney … it really is bargain basement compared to the also Shimano derailleurs on the FX2 never mind the fancy Shimano derailleur on the FX3. The chain audibly grinds as it goes, and the gear changes are noticeably less clean than on the Trek bikes. Yes Shimano Tourney gets the job done, but you’d be slightly wincing as it executes. There is too much grinding metal.
I didn’t think much of T2’s front axle – it’ll be fine, but the engineering isn’t what you’d get on our Treks. The chain, gears and bearings on the Fiido noticeably grind when they turn in a way like on a very cheap bike, and not the fluid and relative silence you get on our Trek bikes. There is a very obvious difference in quality there. I would infer that the wear and tear will be higher on the Fiido, though they do supply replacement parts on their website at acceptable prices. My point is you might get ten years from a chain on a Trek bike at the rate we cycle, and I doubt you’d get five years on a chain from a Fiido T2 bike given the audible wear being put on it. All that said, right now from Fiido’s website a replacement chain costs €24 for the T2. Assuming Fiido remain in business and selling that chain, that seems acceptable considering an OEM Shimano chain for the Trek bikes currently costs €36 and the T2’s chain is 50% longer.
The Fiido’s four inch wide tyres soak up a fair amount of road micro-shittiness which is very pleasing compared to the thin road tyres of the Trek bikes which by definition shakes your bones to their very core every single cycle especially at speed. But the tread on the tyre is noticeably thin which means the tyres will need replacing sooner. I feel this is avoidable for very little extra cost. There is also noticeably more road noise from these fat tyres, and between the drone of the electric motor and these tyres it’s a much noisier experience cycling than with the Trek bikes. In the cities this won’t matter, but out in the countryside with zero noise other than nature … well, the extra noise is unfortunate.
Cheap bikes tend to weigh more – my daughter’s smaller bike is noticeably heavier than our Trek bikes due to steel vs aluminium frames. The Fiido has an aluminium frame, but it has a whole ton load of frame like the old British made Raleigh bikes used to. On the one hand, you will never, ever, break those frames no matter what you do which was the case for those British made Raleigh bikes and I’m fairly sure is the case for the Fiido T2 Longtail frame. On the other hand, you’re lugging around many unnecessary kilograms of weight. The electric motor mitigates this somewhat, but consider the same motor on a 15 kg frame – assuming a 80 kg rider, it would be ~20% faster and more responsive. I can see where Fiido are coming from – a few years ago they had bike frames cracking for which they had to do a recall, which undoubtedly led them to be extra conservative about frames. Similarly, Engwe had all those bikes crushed for not being EU regs compliant, so they’ve gone overboard on being EU regs compliant to their overall detriment.
Finally, it’s a small thing but the torque sensor on the 2025 Fiido T2 longtail which is apparently made by ‘Mivice’ isn’t great in my opinion. To be extremely clear, I would choose this torque sensor any day and at any time over the cadence sensors in the bike models preceding. But there is no avoiding that this particular torque sensor ‘Mivice S200’ is not a great example thereof. Its torque detection range appears to have at most five levels over a narrow range. As a result, when at the threshold, the bike unhelpfully oscillates between power levels in a rough sort of way as you pedal. It generates a rough graduation of power delivery e.g. if you are cycling behind traffic held up by a tractor, you need to have a speed matching the traffic. But the Mivice S200 will choose from your pedalling a speed which oscillates between too slow and too fast for the traffic. This causes a fast-slow oscillation, so your bike rides ‘jumpy’. I mean, it works right, you don’t run into the car in front and you don’t hold up the car behind. But it is hardly smooth.
The same lack of graduated range problem also affects the throttle which has a distinctly non linear application of power to how much you push it down. This also causes jumpiness, because the bike lurches forward causing your finger to retract cutting the power, so now you fall forwards again and the power comes back full on.
We all love how torquey this bike is, but sometimes you just want smoothness instead. Engwe have solved this in their 2025 range using a ‘boost button’ such that the default is a smoothed, averaged torque which takes a while to adjust to pedal pressure. If you want it to respond immediately to pedal torque, you hold down that boost button to turn off the low pass filter the bike is running on the torque sensor. This is one way of solving the problem, however I have to think that this is 100% software stuff, it’s possible that Fiido could fix this ride oscillation problem in a future firmware update, and I do hope that they do so.
I should stress that these negatives are all small niggles. There is absolutely nothing showstopper in here. To be honest, the bike is great, it is comfortable to ride, after 125 km on the clock the battery seems to last plenty of distance, and it has plenty of power and torque. Yes it could be better, but like with my solar inverter, it’s less than half the price of Western marks and not far from as good. Western marks are maybe 20% better at double the cost. This is a very good bike for the money.
Where e-bikes will probably go next
Considering that four years from now I may be able to buy another bike under the Irish Cycle to Work scheme, it is worth reflecting on where e-bikes might be four years from now.
The most likely thing will be improvements to that torque sensor – within four years, I’d expect an unobtrusive match of pedalling to velocity without any roughness oscillating between power levels. This seems extremely doable within four years, especially as torque sensors only entered this price range in 2025. I think future budget torque sensors will be more graduated over a longer range, and thus more fluid and less jumpy. I think firmwares will be better by then at figuring out what you’re doing and the most pleasing response. Or, boost buttons could become standard.
The next most likely thing will be battery capacity. Right now for ~€1,400 inc VAT I can get one kilowatt hour of battery capacity. I would be surprised if in four years from now you can’t get two kilowatt hours for the same money given how battery capacity per euro has been trending.
The third most likely thing will be reduction in weight for the same money. That is something Western manufacturers have tended to focus upon once they maximise every other cost-benefit adjusted feature from their perspective. I would be surprised if Chinese manufacturers don’t follow the same path, and it does have advantages in terms of handling and efficiency.
The fourth thing is suspension for the rear as well as the front. As much as those low pressure fat tyres soak up the micro-shittiness of the roads, they can’t do much for the potholes and the sometimes very rough road surface. Then the front suspension works overtime, and the whole bike still shakes which is neither good for it nor is particularly comfortable for me. If the rear wheel had similar suspension to the front, that would be great.
Engwe’s late 2025 new models I see all their heavy bike models will now come with dual suspension. That should improve the ride on Irish roads quite considerably. If Engwe are shipping dual suspension this year, Fiido surely will next year to keep up.
Shock absorbers are heavy, and any bike with them will always be heavy. Fitting to both wheels you’ll never see the weight below 30 kg without using exotic materials. A 40 kg bike isn’t going to be much heavier with suspension added to the back, and given the improvement to the rider I’d welcome Fiido catching up to Engwe on that.
How the Fiido T2 longtail rides
I’ve only done around 125 km at the time of writing on this bike, so I can say nothing about longevity nor reliability other than nothing has broken yet over some very rough road at speed with a heavy bike.
Here are two routes from my usual cycling route roster with the push bike. The first is that you cycle out to one end of Analeentha greenway, do the 5 km of the greenway which is off road, then cycle back. The second is that you cycle pretty much entirely up hill to behind the nearby quarry, where you get some excellent views, and then it’s downhill from there.
I’ve ordered these as 1A, 1B and 2A, 2B where A is on my Trek FX3 push bike, and B is on the Fiido:

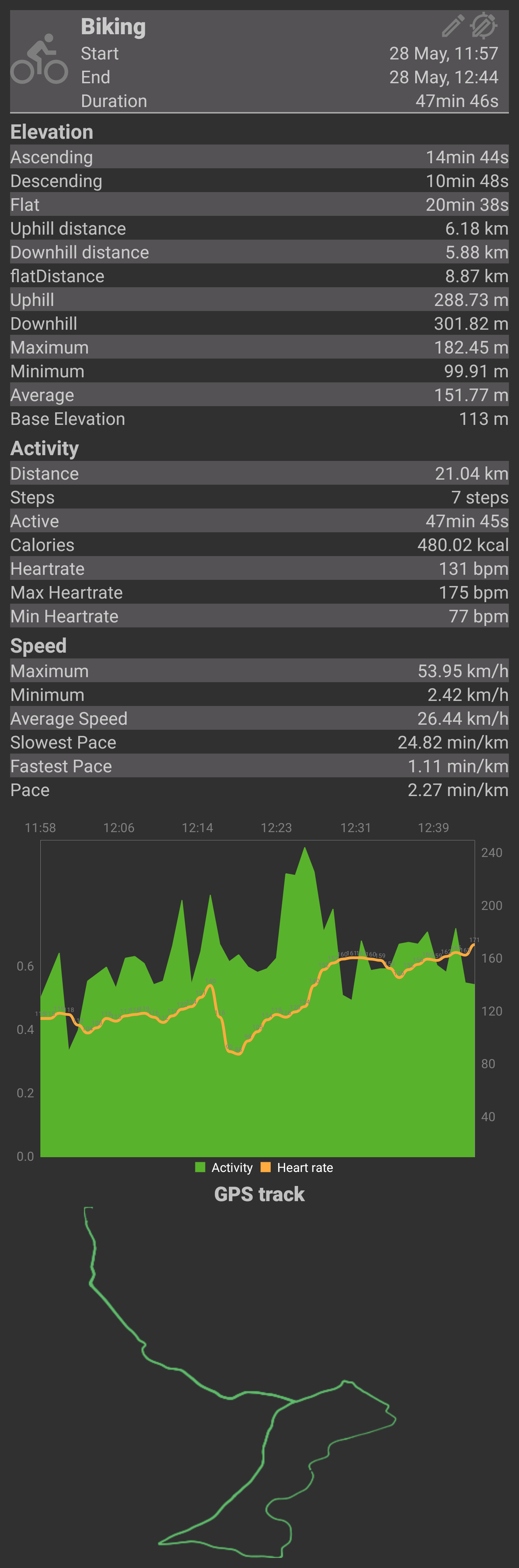
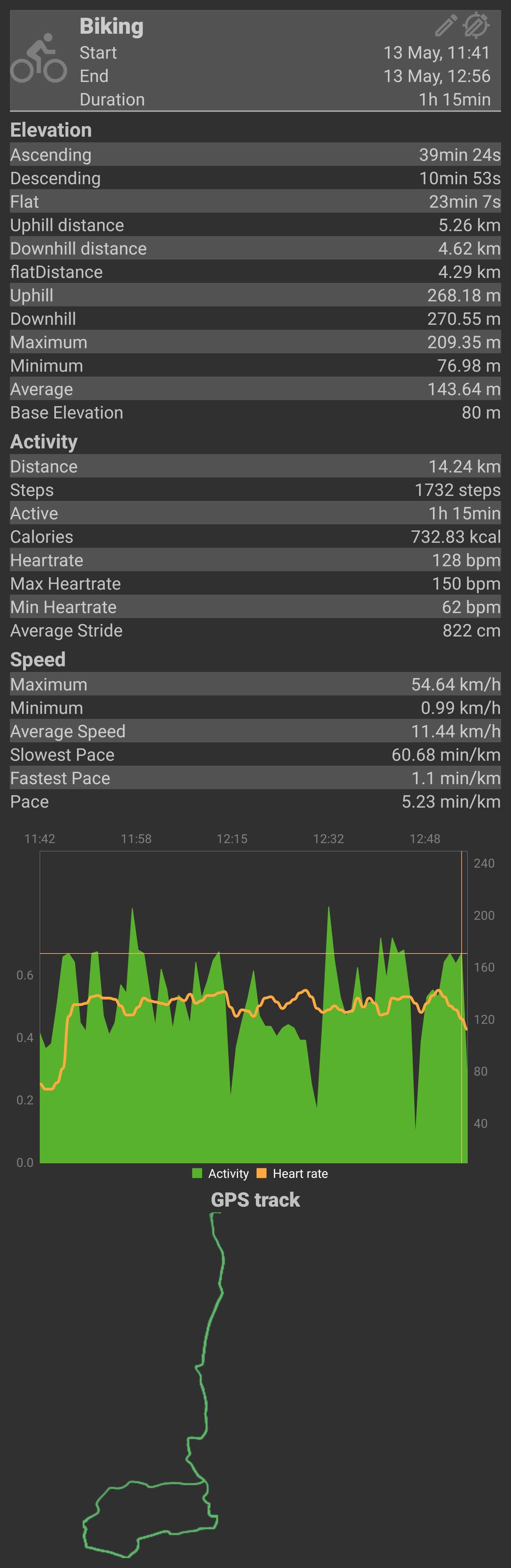
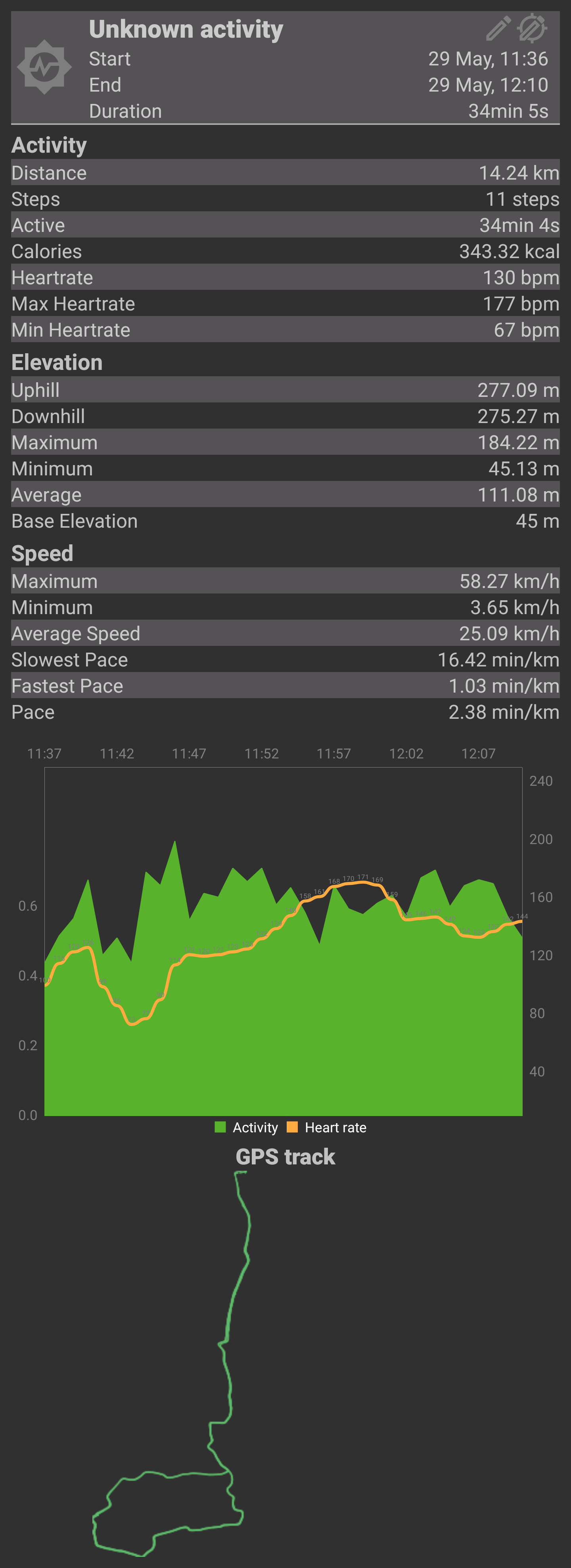
For the first route, on the push bike it took me 1 hr 43 min though in years past before I got fat I could do it in 1 hr 27 min if I remember rightly. On the e-bike, it is a mere 48 minutes. As the average velocity shows, I did a touch above 25 kph average which would appear to be illegal – but in fact that’s because I absolutely hammered the greenway which is off road and downhill. You might notice my peak heart rate for the Fiido ride is very considerably higher than for the push bike ride – that was adrenalin. That greenway is covered in loose stone, it currently has lots of foliage blocking your view around corners, and there was quite a lot of ‘oh shit brake’ followed by ‘max throttle’. This does get the blood pumping!
(I felt bad to do the Analeentha greenway so quickly. It is very pretty. On the push bike, I normally just leave it roll slowly downhill under gravity and I look at the wonderful sights along the way)
For the second route, on the push bike it took me 1 hr 15 min and on the e-bike 34 minutes. Average speed again looks a touch over 25 kph despite me being always on public roads – this is because the bike powers up the hills at 25 kph, the legal limit, and goes rather faster than that downhill under gravity.
I reckon I did about 38 km on these two trips since I charged the battery, so I put it back on the charger and according to the watt meter, it consumed 578 Wh at the socket to bring the battery to full. Assuming ~15% of that was wasted to heat, the battery might have been about half full, despite that the bike showed two out of five bars of charge (40%). I read online that the bike does have a limp home mode and it reserves the last 20% percent of battery capacity for limp home, but I don’t know if that is included in the meter shown. If the meter does represent the whole capacity of the battery, I reckon it uses about 13.2 watt hours per km. Interestingly, the very best EVs in real world testing (not what their manufacturer claims) currently use almost exactly ten times that at 140 Wh/km, and the best of affordable EVs are currently above 150 Wh/km. E-bikes are a far more efficient electric transport.
Having done those two small tests, I then went for the gold standard test:
- Cycle from Dromahane to Bweeng.
- Go up Bweenduff mountain, emerging in Lahern Cross.
- Cycle from Lahern Cross to the base of Mount Hilary.
- Go up Mount Hilary, emerging near Banteer.
- Reach the site in Banteer, take a short break, then cycle from Banteer back to Dromahane via the quickest way possible.
If nothing goes wrong, that is a round trip of 50 km, which leaves a little safety margin.
Well, I can tell you things did go wrong. Here is the route I actually did which I had to reconstruct because the GPS route capture didn’t work due to me fat fingering the recorder:
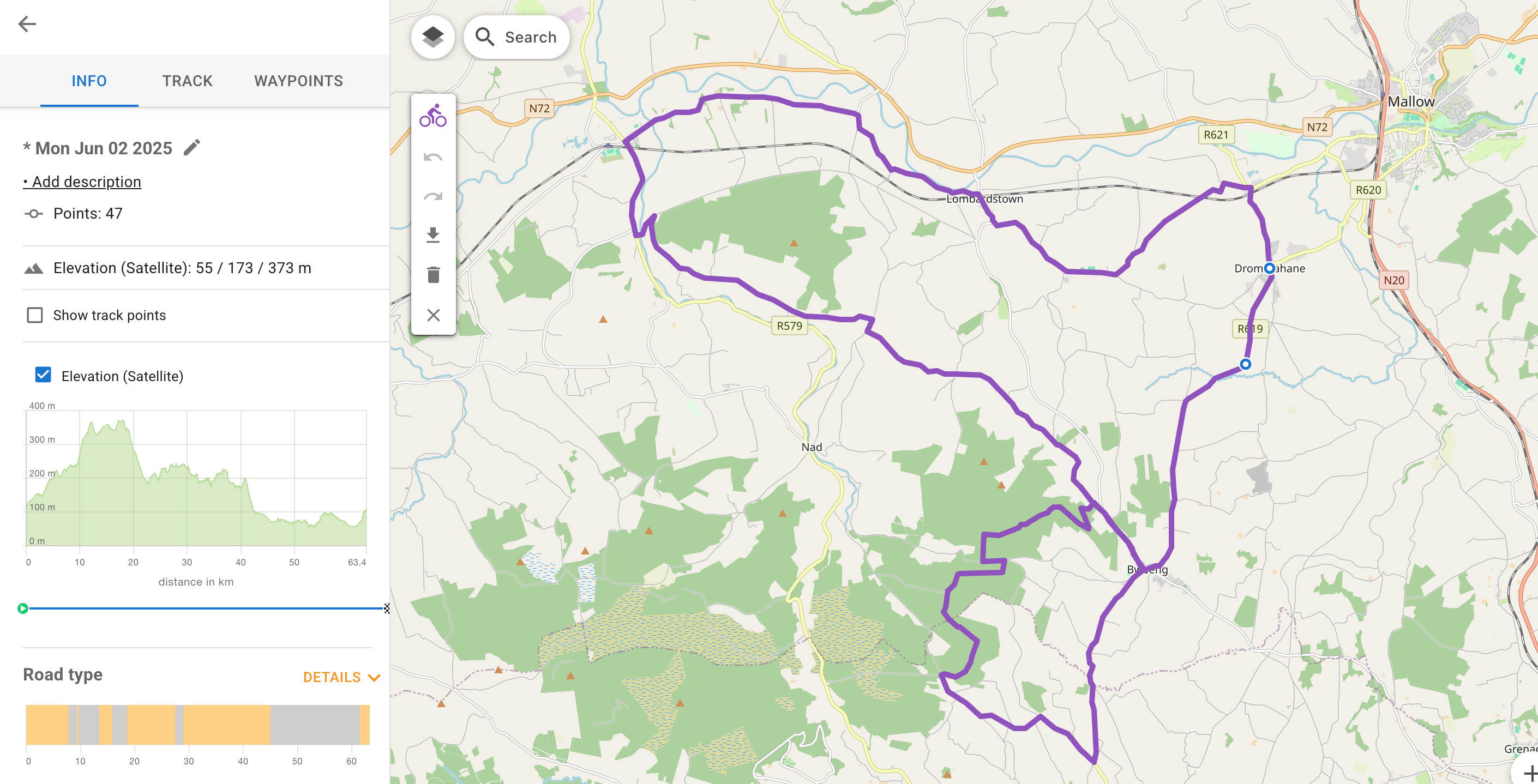
Due to me getting lost on Bweengduff and accidentally heading south, the bike thinks I rode 48 km to reach the site (it slightly undercounts according to the GPS recorder, but isn’t far off). I didn’t fat finger the recorder for the trip home, and that was 19 km making a total of 67 km, with one mountain ascent rather than two. The watt meter says the charger consumed 894 Wh to restore the battery to full, so maybe 775 Wh was consumed by that trip which is 11.6 Wh per km. Given the single > 300 metre ascent, I think that’s pretty good going – though during the ascent, the motor overheating warning appeared and it reduced torque considerably, though not enough to stop the bike.
The bike drops quickly from five bars of charge to four, and takes longer to drop to three, then two. I reached one bar about half way through the cycle back home. If 775 Wh was all that was actually consumed, the battery still had more than 20% in the tank and hence I never saw limp home mode, which would match it happily powering me up the steep hill just before home without complaint. Fiido claim that the bike does under 10 Wh/km on mostly flat if it’s 27 C, and given the 15 C temperature and the > 300 metre ascent, that range claim actually seems plausible.
The gold standard test had me going both up and down steep gravel tracks. I didn’t disable the EU speed restrictions at any point during this test to preserve battery longevity, however I certainly got up to 60 kph going down hill on gravel just from gravity alone.
Yes I did just say I did 60 kph on gravel. That would be nearly guaranteed death on the Trek bikes. On those fat tyres, it was surprisingly safe feeling, even going around corners and braking. When I braked at the end when it reached a main road, the bike stopped in plenty of time despite the speed and the gravel flying everywhere.
The Fiido T2 isn’t supposed to be used as a gravel bike. But it’s a damn fine gravel bike. I had a lot of fun on it on Bweengduff, and I would be surprised if I don’t take that bike up a gravel pathed mountain again soon before the kids exit school.
What’s next?
As my company may not earn money again for a while, we ought to exercise in full our options for utilising the Cycle to Work scheme by Megan also getting an e-bike. She wants a folding one she can easily get up the stairs at her work, so it probably ought to be not too heavy. Here are the current mid 2025 options for direct to consumer Chinese folding e-bikes, with bold for the best feature and underline for the weakest feature:
Bike | Price | Battery | Weight | Claimed torque | Suspension | Tyres | Gears | Notes |
---|---|---|---|---|---|---|---|---|
ADO Air 20 Pro | €1,499 after discounts | 346 Wh | 18 kg | 40 Nm rear two gear drive | Front wheels only | 20 inch by 2 inch | None | appears to surcharge delivery to Ireland and not anywhere else in Europe, including Britain |
Engwe L20 3.0 (2025 edition) | €1468 | 346 Wh | 33 kg | 75 Nm rear drive | Both front and rear | 20 inch by 3 inch | 7 speed Shimano Tourney | |
Engwe P20 (2025 edition) | €999 | 346 Wh | 18.5 kg (excludes rear rack) | 42 Nm rear drive | None | 20 inch by 2 inch | None | |
Fiido D11 (2025 edition) | €1,098 | 418 Wh | 22 kg | 40 Nm rear drive | None | 20 inch by 2 inch | 7 speed Shimano Tourney | launches in July. Are the mudguards bundled? |
Fiido X (2025 edition) | €1,398 after discounts | 418 Wh | 22 kg | 40 Nm rear drive | None | 20 inch by 2 inch | 7 speed Shimano Tourney | has annoying battery lock; rear rack obscures rear light; front light doesn't point with the steering; locking mechanism isn't as good at the D11's; D11 is a good bit cheaper for otherwise identical spec |
Apart from the Engwe L20, these are all 36v systems rather than the 48v system in my cargo bike, so you get a good bit less torque. Apart from the weight, that Engwe L20 3.0 looks amazing – had I not specifically needed a cargo bike to fit two children I’d have gone for that, albeit I would miss the inability to remove the EU power restrictions. I wouldn’t want to lift 33 kg up any stairs though, but for getting it into the boot of a car it would be acceptable and I suspect they’ll sell loads of those for that price and featureset. I mean, if it can fit into the boot of a car, even at that weight you could totally take it for off road riding up and down mountains etc.
If one does want to lift it up the stairs, it looks like the ADO is the first pick and probably the Fiido D11 is the second pick. The ADO’s two gear motor, carbon belt drive and front suspension within an 18 kg package is impressive, even though the battery is a touch on the low side (but plenty for Megan’s commute). I’ve sent an enquiry to see what can be done about that Irish delivery surcharge.
I hope you enjoyed this unexpectedly long post about purchasing an e-bike. I fully expect to use both my push bike and e-bike going forth. They’re actually orthogonal use cases, despite the apparent similarities. After that 67 km trip I was quite, quite sore and it felt like I’d done a similar time, if not distance, on the push bike. So even with the motor assist, they are a fair workout. I’ll be making use of that this summer if the weather permits me.
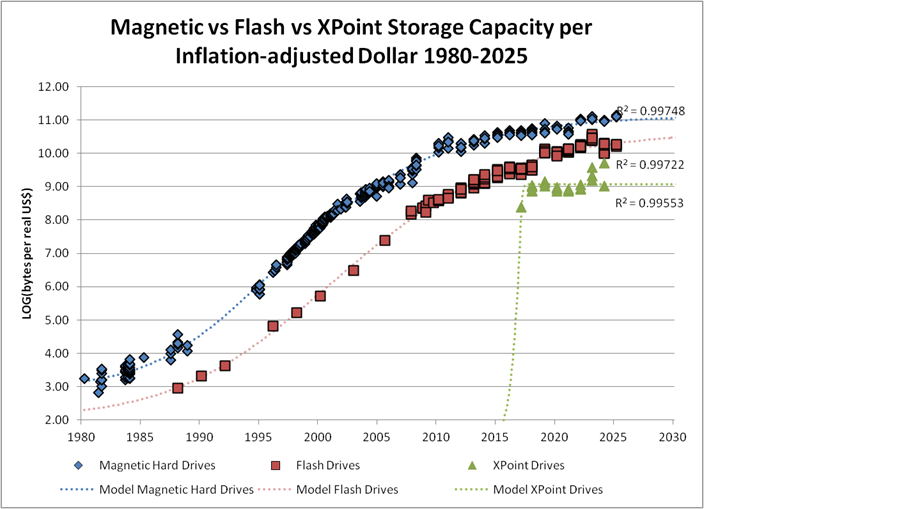
Raw data: http://www.nedprod.com/studystuff/SSDsVsHardDrives.xlsx
You will note that I have stopped collecting prices for Optane drives – historical inventory for them has been sold, and you can’t really get them new anymore. Nor is there any close substitute. I’ll keep the historical data on the graph for now in case somebody does launch new storage with affordably priced non-volatile memory based storage. It’s a real shame how Optane went, had Intel not messed it up so badly, it should have replaced flash for storage.
This year is a normal looking year – spinning rust storage has become quite a bit cheaper, while flash storage has become quite a bit more expensive. It is, however, anything but a normal year because this year’s prices include the effects of the 10% import tariff currently being applied within the United States.
I ummed and awed about whether to try removing the effects of those taxes to keep this year’s figures comparable to previous years. But then this graph is in inflation adjusted US dollars, so we are by definition heavily tied into US economic specifics in any case. And they now have an import tariff making electronics more expensive. So I decided to not attempt to adjust anything. This graph is for the US economy and everything about that economy in each year.
It turns out SSDs are almost exactly 9% more expensive than last year. If you include inflation, it is 7.5% in real terms. Not quite the 10% tariff tax, but undoubtedly a fair price increase.
Hard drives, on the other hand are 28% cheaper including the tariff and excluding inflation. If you include those, they’re more like 40% cheaper than last year, which is getting towards half price. That’s an enormous price decrease in a single year, and most of it I think can be explained by a huge slump in demand for hard drives.
This time two years ago I predicted a recession would cause storage prices to tumble. Here looks like that recession, but so far it hasn’t appeared in the wider US economy, though it has in the wider European and Asian economies.
As regular readers here will remember, I recently picked up a factory recertified 28Tb hard drive recently for a dedicated AI inferencing machine for the site’s security cameras. I got that drive delivered for €400. That might seem a lot, but minus sales taxes (23%) and delivery (maybe €30) that 28Tb enterprise hard drive cost about €300. That same drive cost nearer a grand after taxes this time last year. It’s madness just how much hard drive prices have fallen in a single year. I can’t remember anything like it in recent memory.
During the past month that I’ve known a period of unemployment was coming, I was very busy planning what I’d be doing, getting my affairs and finances in order, and wrapping things up at work so there would be a good hand off. I was very much looking forward to being free of this two metre squared space I have been tethered to for so many years now. However, now unemployment is actually here … I must admit feeling a certain bittersweetness.
At the time, I worked very hard to get into Monad, more than perhaps any startup I’ve ever campaigned to get hired into. I was very keen on the proposition (a better implemented Ethereum), I thought the founders were the right mix to make it happen and therefore a good bet, and I wasn’t unaware that my participation in this project if successful would slightly change the future of all mankind, so my work there would have genuine true real long lived impact.
I had hoped to be contributing until mainnet launch, but after the Series A round the founders decided to localise my part of the workforce into New York and they now had the means to do so. I interviewed my replacements, and I was well aware that I was likely putting myself out of a job at the time. They’re the people which will take this to the end.
As I’ve been part of half a dozen startups by now and therefore more experienced than most startup founders, I’ve often said to startup founders that the people you need to bring you from tiny to small are often not the people you need to bring you from small to big. In my previous roles in startups, I tended to be retained across that transition as many others were let go. This time round, it was not the case, I ended up being one of those surplus to requirements. I am grateful that they kept me on as long as they did, and that they have retained me until the Autumn to hopefully see this thing through from the coalface.
I wish Monad/Category Labs the very best of luck with their mainnet launch, and my genuine gratitude to their founders for taking a chance on me – who was their first international remote hire of many since. I hope I was useful as I pitched to them at the time that I would be.
For the past eighteen months there has been headcount reduction in my industry, and in the past six months that rate has been increasing. When I go on LinkedIn right now, I see many high end devs I know personally who are unemployed, and they are not finding new work at whatever pay rates they’ve been willing to currently accept. A few weeks ago I began noticing lay offs even in AI, which until now has been insulated from the general tech industry recession.
I certainly think another year of tech industry downsizing remains. They over-hired during and after the pandemic, and the revenues just aren’t there to support that much workforce at those pandemic elevated pay rates. They therefore will keep downsizing until average pay levels get low enough that it makes business sense. We have a while to go on that I think.
Tech tends to precede the wider economy, so tech gets a recession first and the wider economy follows after. This has been the longest delay between tech recession and everybody else recession by far in my lifetime, but only from the perspective of the Anglo-Saxon countries. In Central Europe, the everybody else recession followed the tech recession within the traditional delay. What’s different this time is that the everybody else recession has not begun yet in the US, and therefore not in Ireland (much of whose economy is US multinationals).
I think much of why has to do with the US running such a massive deficit – they are borrowing at wartime levels to juice their economy and have been doing so for so many years now that the situation has become detached from normal economic fundamentals. Historically that will turn, eventually, into an especially deep economic collapse along the lines of Argentina which was once one of the richest countries in the world.
I’ve already talked about all that here before, and I don’t have much new to say about it. At some point the debt will need to be paid. Between now and then, it’s entirely possible that the US can carry on borrowing 8-10% of GDP per year for several more years to come. So detachment from economic fundamentals may continue for a while yet, indeed in the Anglo-Saxon countries the tech industry may exit recession into some sort of very weak recovery before the general economy enters recession.
The Irish economy may contain an unusual proportion relative to its size of the US economy, but it is more strongly tied to the European economy than the US economy overall. There are big market shifts happening in Europe. We’re about to build an absolute ton load of weapons all of which will require lots and lots of system engineers like me. The sixth generation European strike fighter is very noticeably completely independent from the US. It likely will be developed by a consortium of the major European powers and Japan and Australia (Canada currently wants to join after US threats upon its sovereignty, but I don’t think that will survive long term after the current US administration exits – after all, such a project has a half century long time horizon). Like the competing US, Chinese and Russian sixth generation strike fighters, it will be more an nVidia CUDA based supercomputer than airplane. As the programming languages well supported by CUDA is very limited (and does not currently include Rust), that could turn into stable long term employment for people like me who specialise in C, C++ and Python.
As this is Europe, pay rates will be a fraction of those elsewhere. But stable – or any – income is better than none. So I think Europe may be an exception to the wider pan-tech industry malaise if you’re a systems engineer. Ireland not being in NATO nor having any security clearances will mean Irish citizens won’t be allowed to work on anything secret, so we’ll likely be given dual use technologies like drones, resilient communications, and perhaps core stack stuff like deterministic runloops and work dispatchers. Anything secret will be reserved for citizens of the participating countries. I guess we’ll find out.
I’ve found myself pondering what do I want in my next employment? I do genuinely actually find AI appealing, and no I’m not lying nor faking that sentiment. I think AI will not solve 95% of the things everybody is trying to use it to solve. But that other 5% … I think it could be transformative to my personal productivity, and possibly to enough others to matter overall to an economy wide picture.
However, I must be realistic: I am forty-seven years old, and almost all of AI does not make direct use of the low level skillsets I specialise in. I am therefore unlikely to be a good fit for getting into AI at my age and skillset. Also – to be blunt – I think the AI balloon is beginning to deflate in any case anyway, and then it’ll go through a period of being out of fashion until it comes back into fashion again. Such is the tech economy.
Having pondered on this for the past month … why on earth hasn’t IoT become an expanding bubble yet? I, like many others, feel that IoT ought to be an exponential growth opportunity like AI has just been at some point. But we never seem to reach that point. Rather, IoT seems to just constantly keep incrementally creeping forwards and inwards subtly and never experiencing a ‘break out’ moment as it infests ever more parts of the global economy and human existence in general. Maybe those are its dynamics, who knows?
I guess what I’m really asking here is ‘where will the tech industry go next?’ i.e. what inflating balloon do I need to hitch myself onto before it rises? I have been relatively successful and/or fortunate in predicting/happening to be right place right time so far. I need to repeat that magic. I will admit that at the time of writing, apart from European weapons systems, I can’t think of anything likely to be the ‘next big thing’. Here’s hoping some clarity arrives on me in the next few months.
What’s next?
One of my long time unfinished projects has been a dedicated AI inferencing security camera PC. I combined a fifteen year old case with a ten year old PC guts and a ten year old second hand enterprise nVidia AI inferencing card plus a 28 Tb recertified hard drive to build a top of line security camera monitoring and recording box. This box has been built, debugged, and tested. I just need to write it up. There will surely be a post about that here soon.
Believe it or not sixteen months after I shook hands with my replacement builder a first draft of construction detail has turned up. Yes of course it would appear now when I’ve lost my job. In any case, there is now a reasonable expectation that a final quote could be issued some time in the next six months. I almost certainly cannot take a decision on build vs no build until the Autumn, but if we could get that final quote before then … that would be great as there would be actual forward progress at very long last. There will surely be a post here about the first draft of construction detail etc at some point.
The differential pressure sensors I mentioned some posts ago have turned up and those will need testing. I have also acquired an anemometer so I can finally say what air flow is passing for given readings of those barometric sensors. That will likely also result in a post here.
Finally, the next post will be all about cargo e-bikes, as I already have written that post due to buying and testing a cargo e-bike. All will be explained in that post!