What came back to us is this first draft of a joist design:
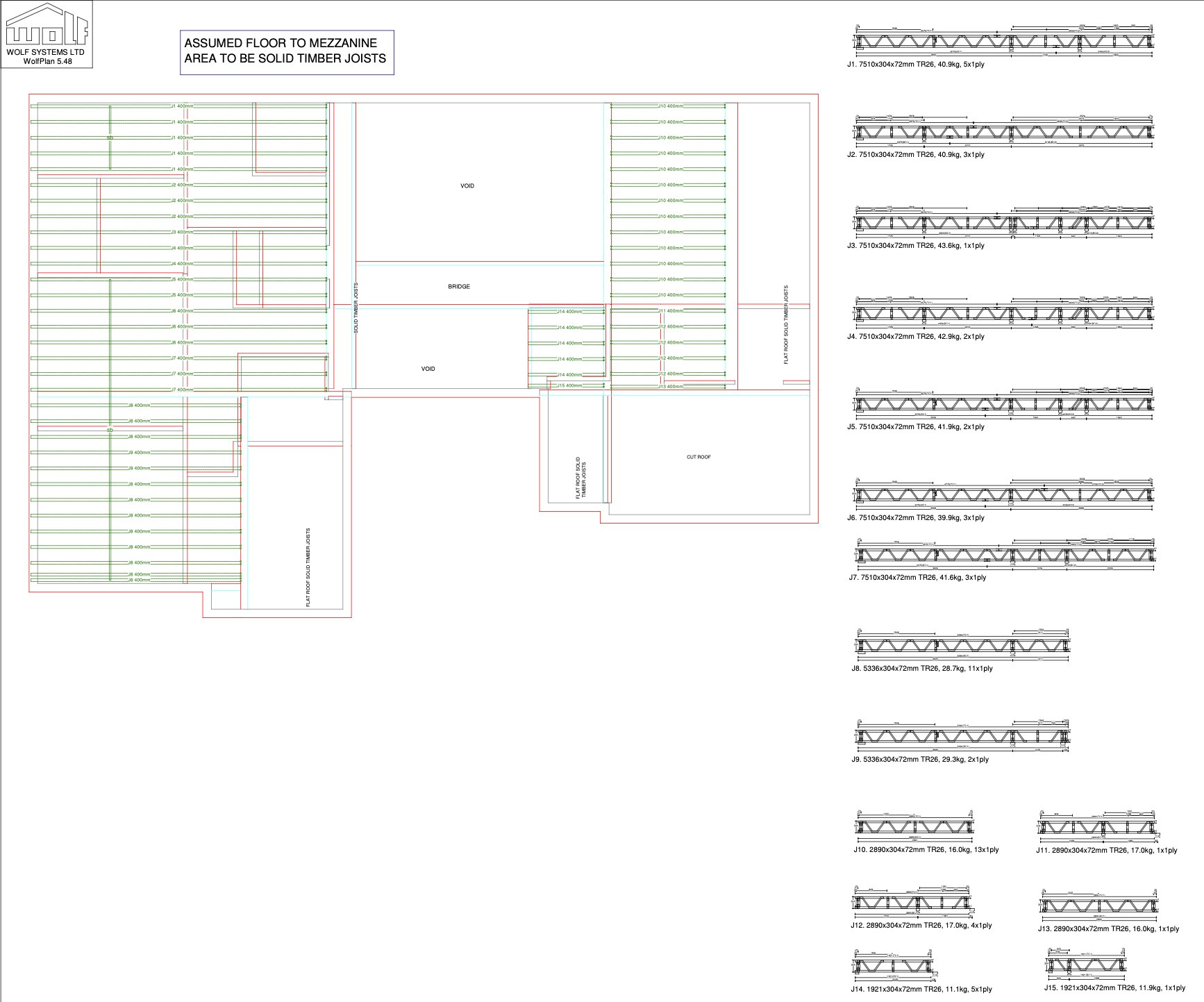
… which, obviously enough, arranges all the joists left-right. Which, for any normal house would be fine, but in our specific case we have a highly insulated fresh air duct for the ventilation because it carries most of the space heating. Which means it’s fat, especially in the hallway just outside the utility room where it comes from the MVHR. There, the fresh air duct is approx 280 mm in diameter after the insulation, and myself and my architect had solved this by running the joists up-down just for the hallway, and left-right elsewhere.
Normally you should always orientate your joists in the same direction as the ridge of your roof, so if the ridge runs left-right as it does in this house, so must your joists. This is because the roof trusses will be perpendicular to your ridge, and you then want the floor joists to be perpendicular to those again to brace them.
However, due to the vaulted areas in this particular house, we have two steel portal frames either side of the vaulted area with steel beams pinning both of the house ends to those frames, and then two more steel beams pinning both portal frames together (really this is a steel frame house). Because the steel takes on most of the bracing work, you should be more free with the joist orientation. This is why myself and my architect took advantage of that during duct routing.
Unfortunately, my TF supplier was adamant that if we wanted up-down joist runs in the hallway, we’d need to fit steel, and that steel would need to be custom designed by a specialist engineer, and coordinated with the joist design to fit. That sounded (a) expensive, no designer in this current busy market is willing to take on new work unless their fees are at least €5k and steel is hardly cheap either and (b) it would be months more of delay, at best.
So that now meant we needed to get those ducts through a 304 mm tall joist which has an absolute maximum of 300 x 210 mm clearance. Otherwise months more of delay would occur and large unexpected additional sums of money. Wonderful.
High end custom made industrial ducting
Here were the choices before us:
Custom steel joist design. Cost: five figures. Lead time: months.
Increase joist height from 304 mm to 417 mm. Cost: five figures. Lead time: weeks (mainly to redesign all the ceilings). Also: you lose a fair bit of ceiling height.
Instead of insulated circular steel ducting, use high end custom made industrial ducting. Cost: four figures. Lead time: days. Would need a bit of rejigging the duct layout as the 300 x 210 mm pass through limits airflow to an equivalent 160 mm diameter duct.
So option 3 was the obvious one (well, initially I didn’t know how much it would cost, but I asked for quotes got back numbers and now I know it’s four figures of added cost. Painful, but less than the alternatives). Within Europe, there are a number of prefabricated preinsulated duct manufacturers all supplying the standard DIN sizes cheaply, but if you want custom dimensions they get expensive. Indeed, the gap between their cost and the ultra fancy Kingspan Koolduct gets reasonable. That stuff is the second highest end insulated duct on the market, due to it using a special heat resistant and stiffened phenolic foam cut by CNC machine and then hand assembled into the finished form. As the hand assembly is done by western Europeans using foam blown in western European factories, it isn’t cheap. But in terms of performance for the space, it’s very good and much better than can be achieved with conventional fibreglass wool duct insulation:
- @ 10 C, 0.022 W/mK (vs 0.037 W/mK for ductwrap)
- @ 25 C, 0.024 W/mK
- @ 50 C, 0.027 W/mK
- @ 80 C, 0.031 W/mK (vs 0.046 W/mK for ductwrap)
The only better performing duct material is vacuum panel at 0.007 W/mK. It’s superb, but you could buy a fair portion of a whole house with what it costs.
52 mm of this phenolic insulation delivers these u-values:
- @ 10 C, 0.423 W/m2K
- @ 25 C, 0.461 W/m2K
- @ 50 C, 0.519 W/m2K
- @ 80 C, 0.596 W/m2K
I assumed 18.5 m2 of fresh air duct for my calculations (this is pre-recent layout changes). If so, one would leak the following amounts of energy out of the ductwork, thus not delivering it to the outlet if the house is at 21 C:
- @ 10 C, 7.826 W/K, so -86 watts.
- @ 25 C, 8.529 W/K, so 34 watts.
- @ 50 C, 9.602 W/K, so 278 watts.
- @ 80 C, 11.03 W/K, so 651 watts.
Are these losses acceptable? It depends on the rate of ventilation air flow because the losses are fixed to temperature difference, but the amount of energy transported rises with more air flow:
Duct air temperature | 200 m3/hr | 400 m3/hr | 600 m3/hr | |||
---|---|---|---|---|---|---|
Heating | Losses | Heating | Losses | Heating | Losses | |
10 C | -645 W | 11.74% | -1290 W | 5.87% | -1936 W | 3.91% |
25 C | 235 W | 12.814% | 469 W | 6.40% | 704 W | 4.27% |
50 C | 1701 W | 14.41% | 3403 W | 7.20% | 5104 W | 4.80% |
80 C | 3461 W | 16.54% | 6923 W | 8.27% | 10384 W | 5.51% |
I would expect the system to run at no less than 150 m3/hr unless the house is unoccupied, so losses to ductwork of greater than ten percent are distressing. The next Koolduct size up is 60 mm which is 15% better, but now you swap air pressure loss for thermal efficiency. I’ve been a little unreasonable in this design by aiming for a 0.5-0.75 Pa/linear metre pressure loss which is excessively loose (less than 2 Pa/metre overall is what you need to achieve). But it’s for good reason - the boost fans can increase the air flow for a specific outlet or inlet very significantly, and you want enough slack in the ducts to cope. Also, due to me not having the modelling software, I’ve ignored friction, bends and several other factors which cause additional pressure loss over linear metre calculations.
There is also the cost angle: the 52 mm Koolduct costs about €110 ex VAT per metre. The 60mm stuff I would assume would be maybe €126/metre. Given that standard DIN size preinsulated ducts (albeit with EPS instead of phenolic board insulation) cost about €60 ex VAT/metre, one is paying a big enough price premium already to fit these ducts inside the joists.
I think, to be honest, it’ll just have to do.
The new duct routing
So, having digested all of that, I have drawn in to correct scale a potential duct routing with sufficient dimensions for the flows which definitely fit through and between the draft joist layout above:
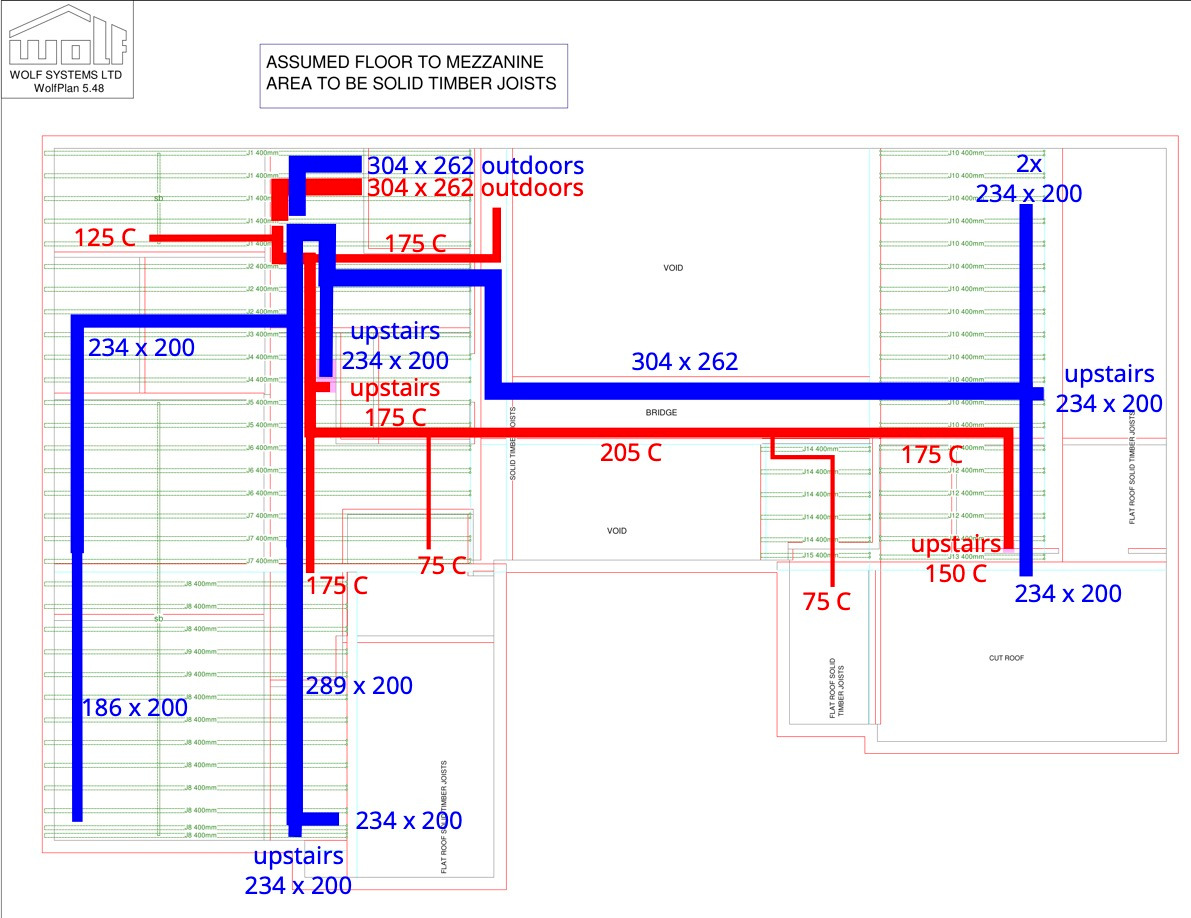
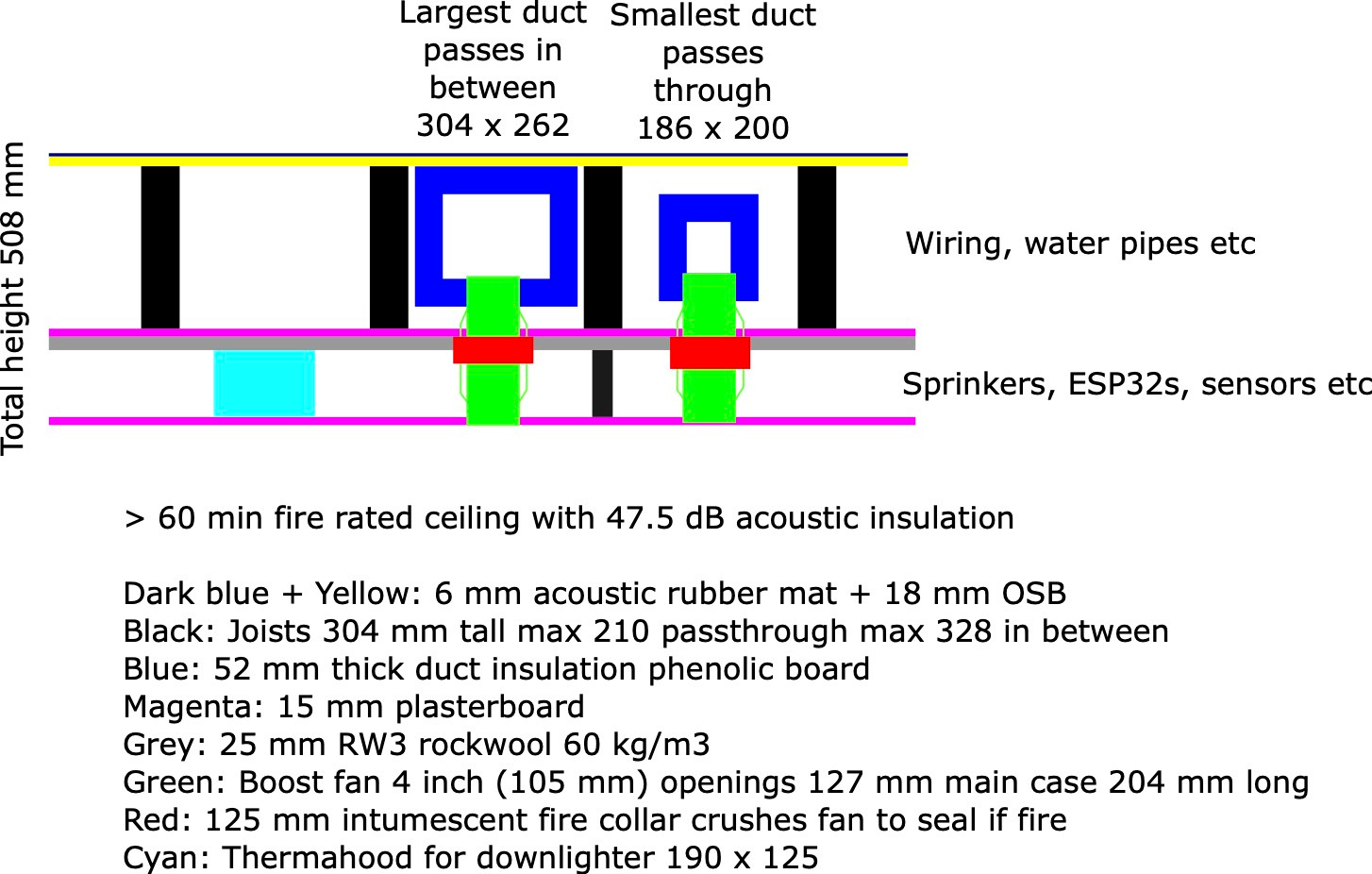
Unfortunately, that’s not the end of it. Obviously the above are not ‘CAD quality’ drawings despite the fact that they are exactly to scale and indeed of identical resolution to the original CAD file (Inkscape is surprisingly good). And in any case, we shall need a 3D design in order to send the exact order for the Koolducts through, because there is vertical detail omitted on that 2D layout.
Hence I’ve come to an arrangement with my architect to do some additional work to turn this into 3D and adjust the joists (in some places they just don’t make sense). Hopefully he can deliver that next week, and then we can unblock forward progress with the joist design.
Here’s hoping!
Raspberry Pi colocation
You may remember my recent post on upgrading my internet server infrastructure in which I said I was researching whether to replace my rented Intel Atom 220 based public servers with colocated Raspberry Pi 5’s. Well here they are nearly ready to be dispatched to the colocation:
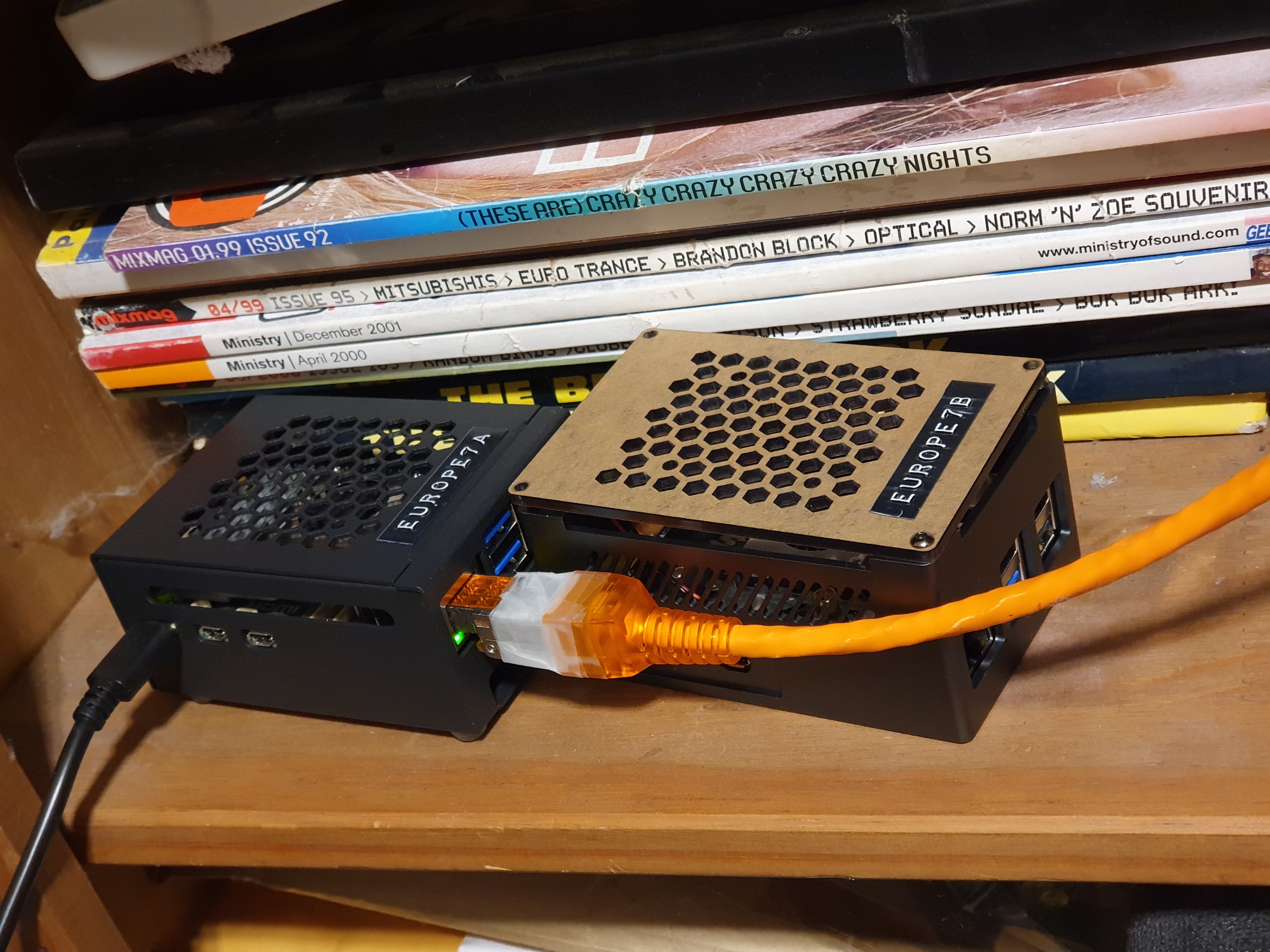
These will be my seventh generation of public internet infrastructure. One will act as primary, the other as failover. Both will be in the same rack so they get a 1 Gbps network connection between them, but external internet will be clamped to 100 Mbit shared with everybody else on that rack. For under €9 ex VAT/month, I can’t complain.
As you are concluding, after quite a few head scratches I got my full public Docker Compose based software stack up and working with offsite ZFS replication running well. They are very noticeably faster than the current Intel Atom 220 infrastructure, plus due to having double of pretty much everything (RAM, SSD, CPU etc) they have room to grow. Barring unpleasant surprise, these should last me until 2028 when the next Ubuntu LTS upgrade would be due, and possibly for a second four year period under whatever the next Ubuntu LTS will be then (28.04?). The aim will be to have one returned, it upgraded, sent back, migrated, then have the second one returned and upgraded. We’ll see how it goes.
I hope to post them on Wednesday – I am waiting for another NVMe
SSD for europe7b
because the one I got off eBay wasn’t compatible
as it turned out (nearly compatible, and it cost me staying up
to 4am one night going WTF? a lot before I realised it wasn’t me
and it isn’t the Pi). So I’ve ordered an official Pi SSD which is
really a rebadged Samsung 991A SSD. Should work very well, and should
arrive on Monday just long enough for me to get the second Pi also
configured and ready for dispatch.
Go to previous entry | Go to next entry | Go back to the archive index | Go back to the latest entries |