Design changes post Passive House design assurance review
Visible changes since the last time I posted computer renders here are few, but quite a lot non-visible did change:
We moved from a 140 mm tinber stud wall filled with phenolic foam to a 300 mm split stud filled with cellulose. This caused the side walls to go from ~0.4m to ~0.5m, which is a lot fatter. The cause was during PH design assurance Robert Ryan our PH certifier found runaway moisture build up in the walls in the humid Cork climate which is our site location. To be clear, it was very close, it took six years in the model for the walls to become saturated due to accumulating more moisture annually than being able to expel it. In the real world, that assembly could have been absolutely fine for twenty years, or riddled with mould and needing demolishing within two. It would depend on the actual weather, obviously. And no shortage of timber frame houses are built in Ireland and are just as close to the margin, and are fine (or not!).
Obviously, had our climate been just a touch dryer e.g. in Dublin, there would have been zero issue. But it just goes to show how careful you need to be with foam insulated timber frames in a humid climate.
Anyway the cellulose airs out much much better. Bob’s modelling found zero moisture build up even if the Cork climate had winter levels of RH for six months of the year. You just need a little bit of wind through the outer cavity, and it’ll dry out.
Obviously due to all the walls getting thicker by a quarter, lots of stuff had to be resized, especially the north curtain glazing which had to shrink in width. This improved heat losses obviously enough, and gave us a nice safety margin for PHPP. Indeed, we used some of those heat loss gains to make other windows a bit wider as we had the energy budget.
Previously, the steel frames had sat within the insulation as foam is rigid and detailing could keep the steel warm. My best understanding is that it isn’t wise to put steel through cellulose (I don’t entirely understand why, google says it doesn’t corrode steel and packs itself very snugly around steel), so our architect moved the steel frames to inside the airtight layer. Hence, we now have steel frames sticking out everywhere.
It could be worse, we knew from the beginning that if we wanted vaulted ceilings, we could be getting exposed steel in return. So we’ve made the best of it, they’ll be painted oxide red and we’ve exposed them everywhere we can so there are clean lines, and you can see how it all hangs together.
As a result of the steel frames coming inside, we had to lose one of the windows in the reading area of the library mezzanine. Bob wanted one more solar panel anyway for safety margin in PHPP to ensure we’d definitely achieve Passive House Plus, so that window has been replaced with an additional solar panel, making thirty-seven in total.
Other than those changes, the house looks as it did before. When Stephen our architect updates all the feedback from all parties solicited to the first release of the draft final plans, I’ll present some screenshots here as barring any surprising changes coming from the structural engineer, that’ll be the final final house design.
Electrical schematics
As we are heading quickly towards the design being written in stone forever, there were a lot of loose ends which needed tidying up.
Firstly, I really needed to get the detailed electrical schematics finished. I kept putting them off, as they’re tedious and time consuming and I’m busy, but earlier tonight I made myself complete every room in the whole house, as I can tarry no further. I still have yet to do the distribution box design and load calculations from tying all the rooms together, but finally I have a schematic with everything every room in the house will have (electrically speaking, anyway). Here are some examples for (i) Master Bedroom (ii) Master Bedroom Bathroom (iii) Utility (which shows all the space heating stuff) (iv) Kitchen south:
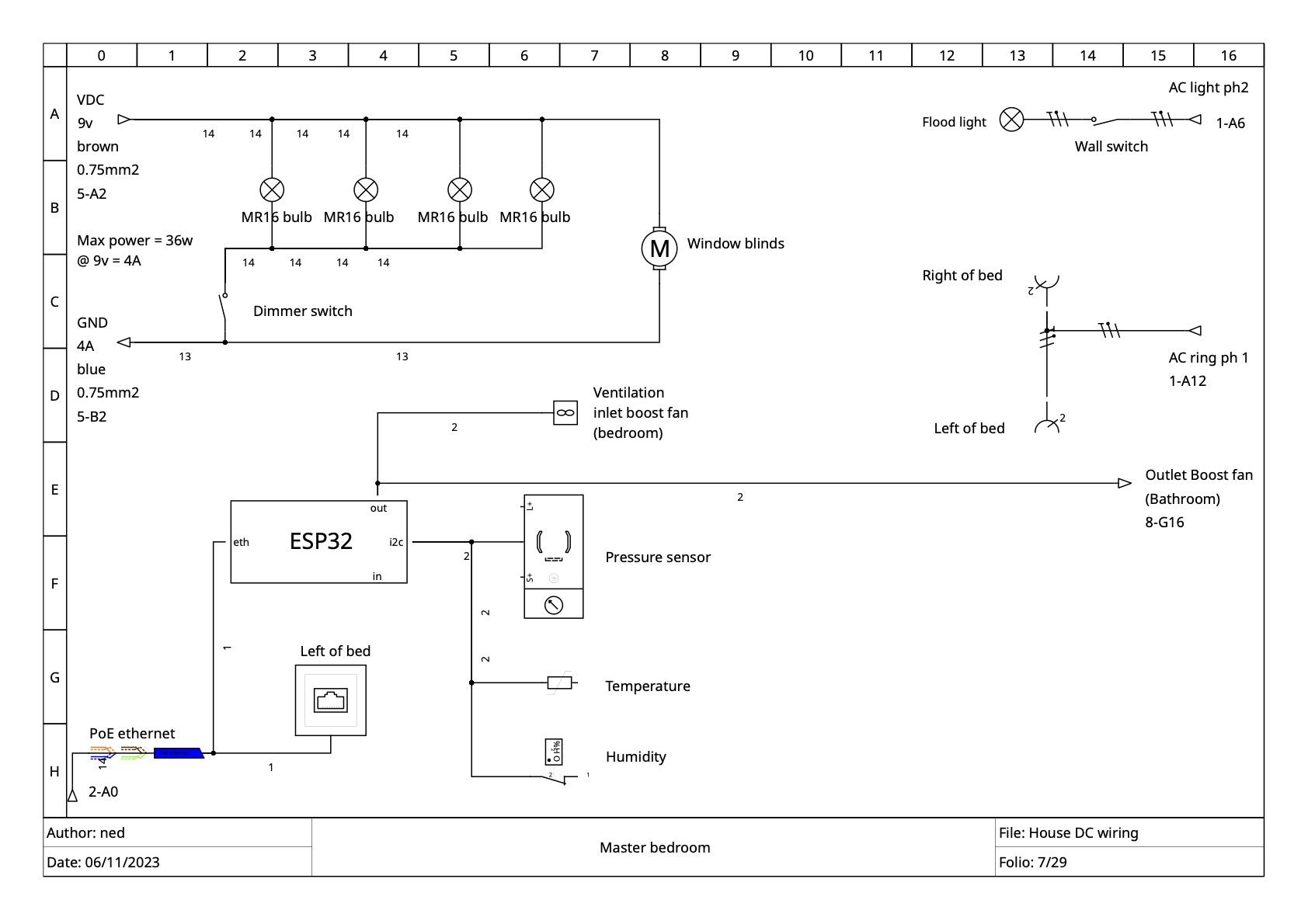
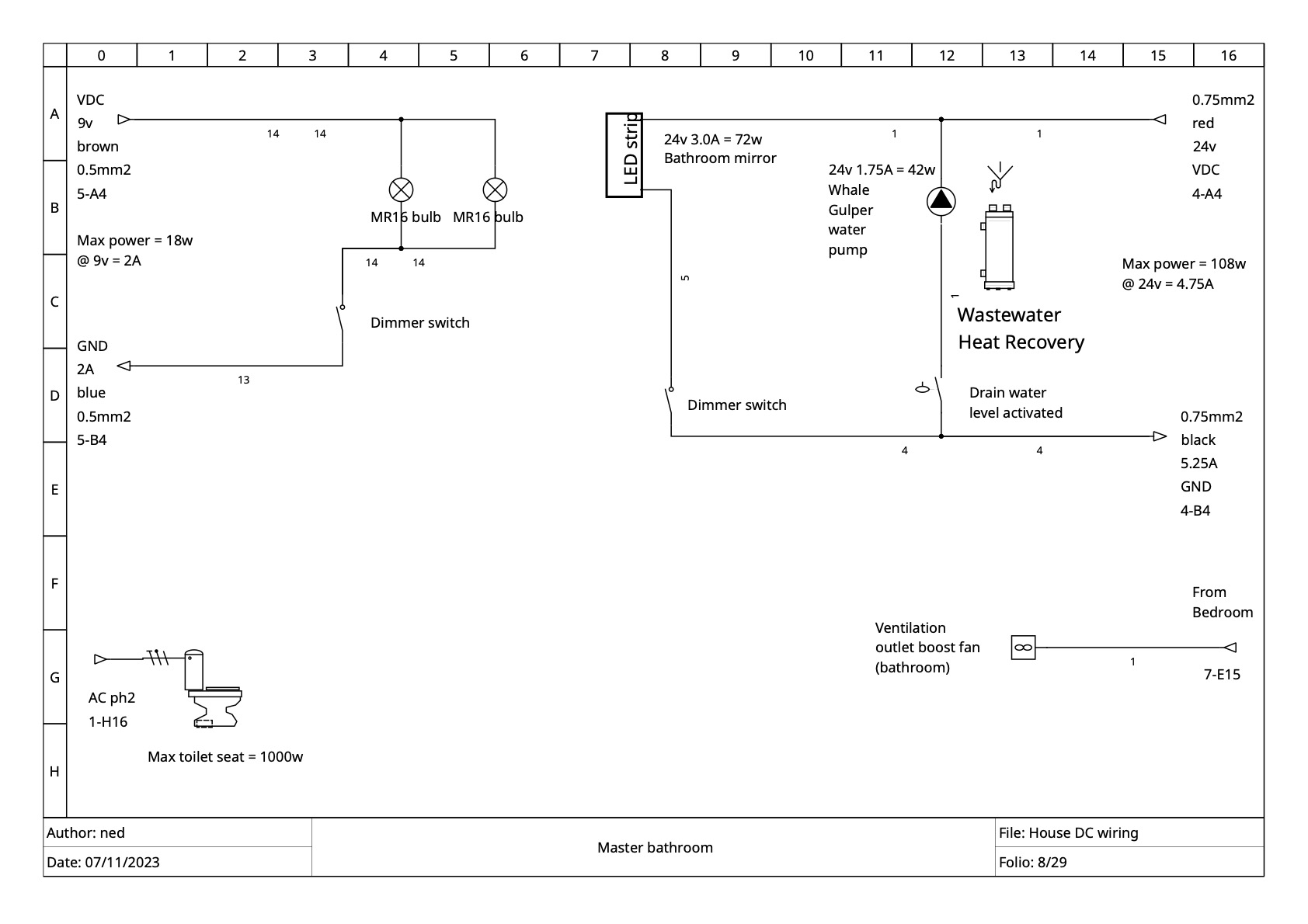
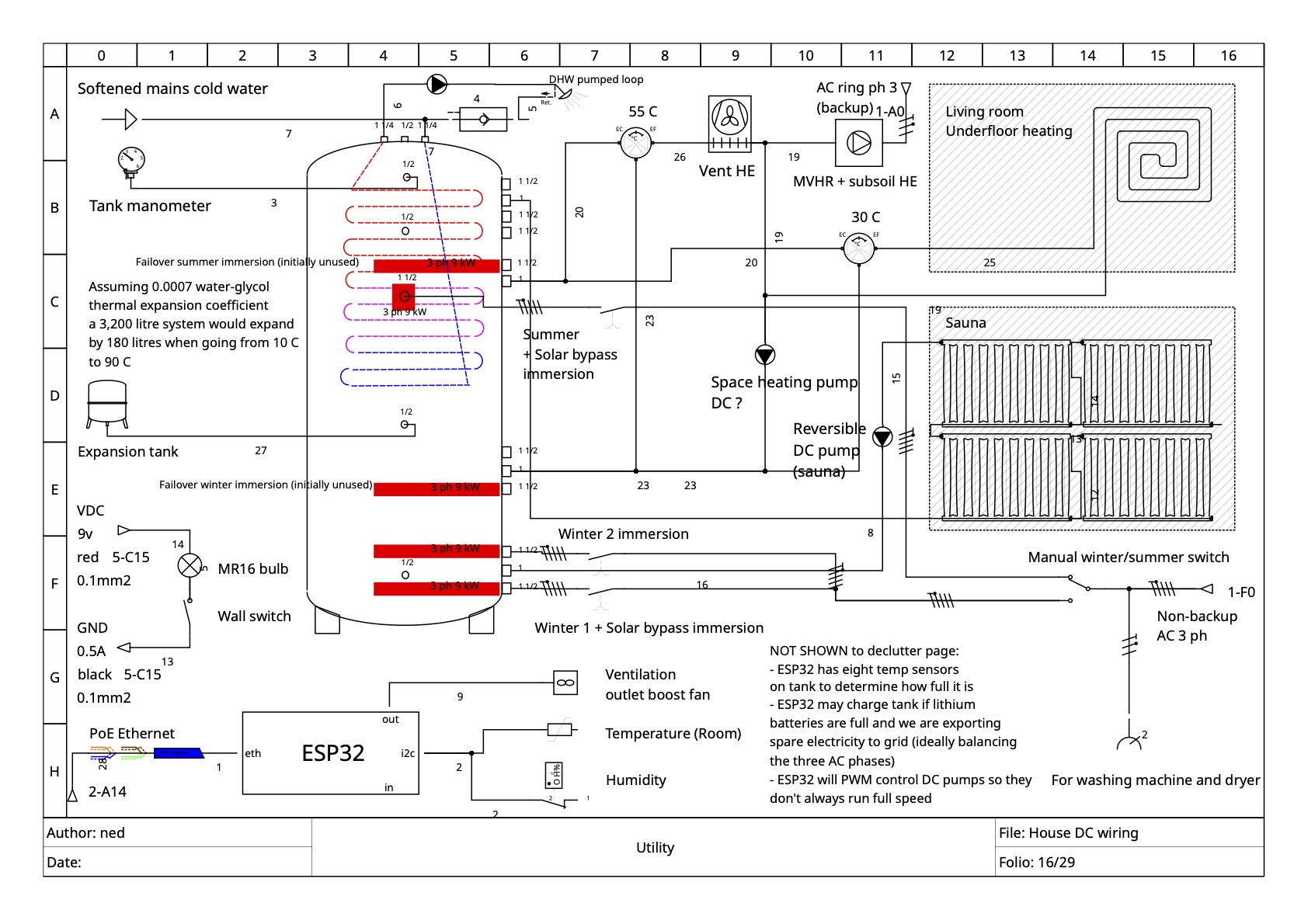
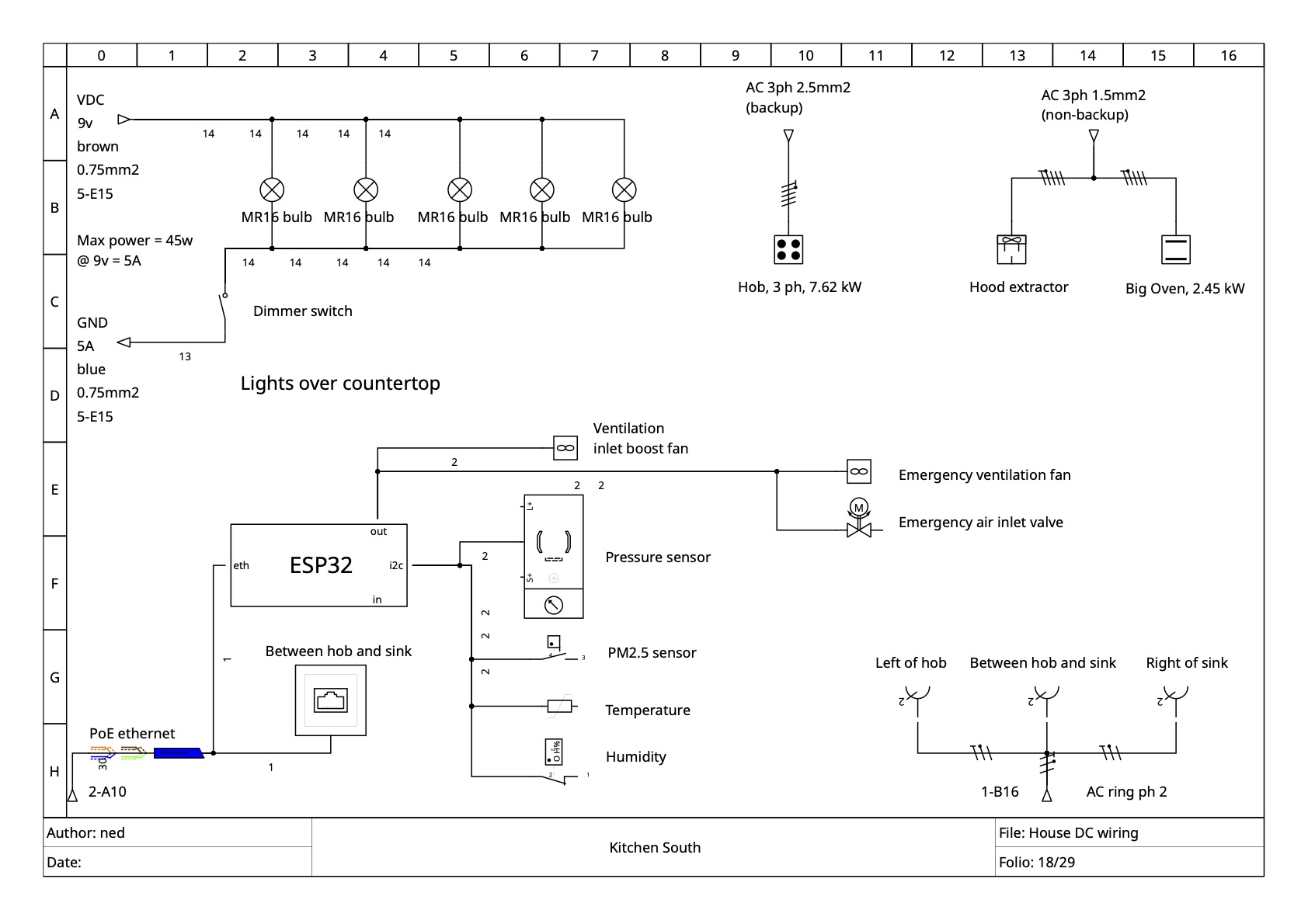
The software I used is QElectroTech. It isn’t too great if I’m honest, there are loads of small annoying bugs and lots of stuff which feels either half arsed or half finished. But it’s free, and it does get the job done. I think the print renderings are especially not half bad, frustrating and tedious as it is to make them in the first place.
As all the socket and light placements have been fixed, I can now design exactly where to trunk the cabling once wire load calculations and distribution box design is done. All that is a few more hours work, the hard part was getting all the rooms done as now I can give a good approximation of what cable trunking will be needed and where, so we can tell the builder and structural engineer exactly where penetrations into the foundations will be e.g. if you need to lay a conduit for some underground cable.
The main entrance door
Another item I’ve been kicking down the road was the front entrance door. Nordan will be supplying all the glazing and doors apart from the entrance door, mainly because Nordan’s entrance doors do not look good. Indeed, their only passive spec entrance door very much looks like a school canteen door. I don’t know who designs their entrance doors, but they should replace them, whomever they are.
Munster Joinery’s only passive spec (u-value <= 0.8) door looks fine from afar, but when you get close to it it does not look good at all. Like most of the composite doors on the Irish market right now, they mould in a wood grain effect to the outer fibreglass, and then paint it with wood paint so from a distance, it does look fairly convincingly like wood. In fairness to MJ, they chose a rough wood grain unlike any of the competitors who have chosen a smooth wood grain. I actually prefer the rough wood grain, but it does make the door look like rough painted wood like you’d get on an eighteenth century cottage. And if it were just that, that would be fine, but unfortunately it also has all of MJ’s quality control issues with trim around windows – you’ll usually find at least one of the trims which doesn’t quite fit, isn’t quite flush, or the paint isn’t even. And this is even in their showroom models. It’s weird, it’s such a small thing to not screw up, but I guess they sell plenty of entrance doors with those issues and obviously the customers don’t care.
The other thing, of course, with painted fibreglass is the paint WILL come off after a few years and then you need to repaint it every few years thereafter. So as much as I appreciate them modelling wood as closely as possible complete with repainting it regularly, I’d rather less maintenance if possible.
Rationel and Palladio are two more sources of composite door with u-value’s below 0.8. Rationel’s website isn’t helpful at saying what door has what u-value, I kinda gave up and moved on to be honest (in fact, most of the big glazing and door manufacturers have REALLY lousy websites, they just show pictures of their products and present no detail which is actually useful like u-values or assembly breakouts). Palladio are of course Irish, they’re the biggest composite door manufacturer in Ireland out of their Limerick factory. Y’know, I really wish all glazing and door manufacturers were like Palladio, they have really comprehensive data about their products all online and all presented in an easy to browse, well categorised format. Every single installation option is shown complete with installation diagrams, assembly diagrams, u-values, materials, all from multiple angles. They are actually by far and away the best for an online presence of any glazing or door manufacturer I’ve seen in Europe. Really really good.
Unfortunately all their doors have a wood print on the fibreglass. I find it looks cheap, it’s too shiny and plasticky looking, and the pattern isn’t quite right. The rest of the door looks fine, no quality control issues like with MJ’s doors, and the u-values come in as low as 0.7 even with a pane. They’re a fine thick door too, 65 mm, which helps offset the lack of heft you get in composite doors as they’re basically 95% polyurethene foam.
Sometime around this point I kinda kicked the whole problem to touch as it was soaking up a lot of time, and I had more urgent issues. Last weekend we went to SelfBuild Limerick and Internorm were there. They had a rather nice looking entrance door with u-values well below 0.8 depending on which assembly you choise. Aha! I thought to myself, despite the lack of a Cork office, perhaps this is the solution?
Well, I went and got a quote after we got back. Now, steady yourself good reader, steel yourself for this: the quote was for €7,584 inc VAT delivered and installed. For a front door. When, the entire house’s passive grade glazing and no less than four other entrance doors comes in for €46k inc VAT delivered and installed. Which makes just the entrance door a whole one sixth of the total cost of all the other glazing and doors.
Needless to say we won’t be taking that option. I did check with the vendor if they had a mistake, and I was told that that thickness (93 mm) to achieve the sub-0.8 u-value was one of the most expensive Internorm has. And yes, it’s a rather nice door, and I appreciate it has three layers of aluminium in there for strength, and it’ll have as a result a nice bit of heft. It’s a superior door. But no way for us. Not in a million years for that kind of money.
So, that returns me to the unpalatable choices before me. I have found a potential light in the darkness however: Northern Ireland’s biggest composite door manufacturer Apeer also mostly produce wood grain effect on their fibreglass, but they do have one option without the wood grain effect, and here it is, along with their hilarious promotional video for it:
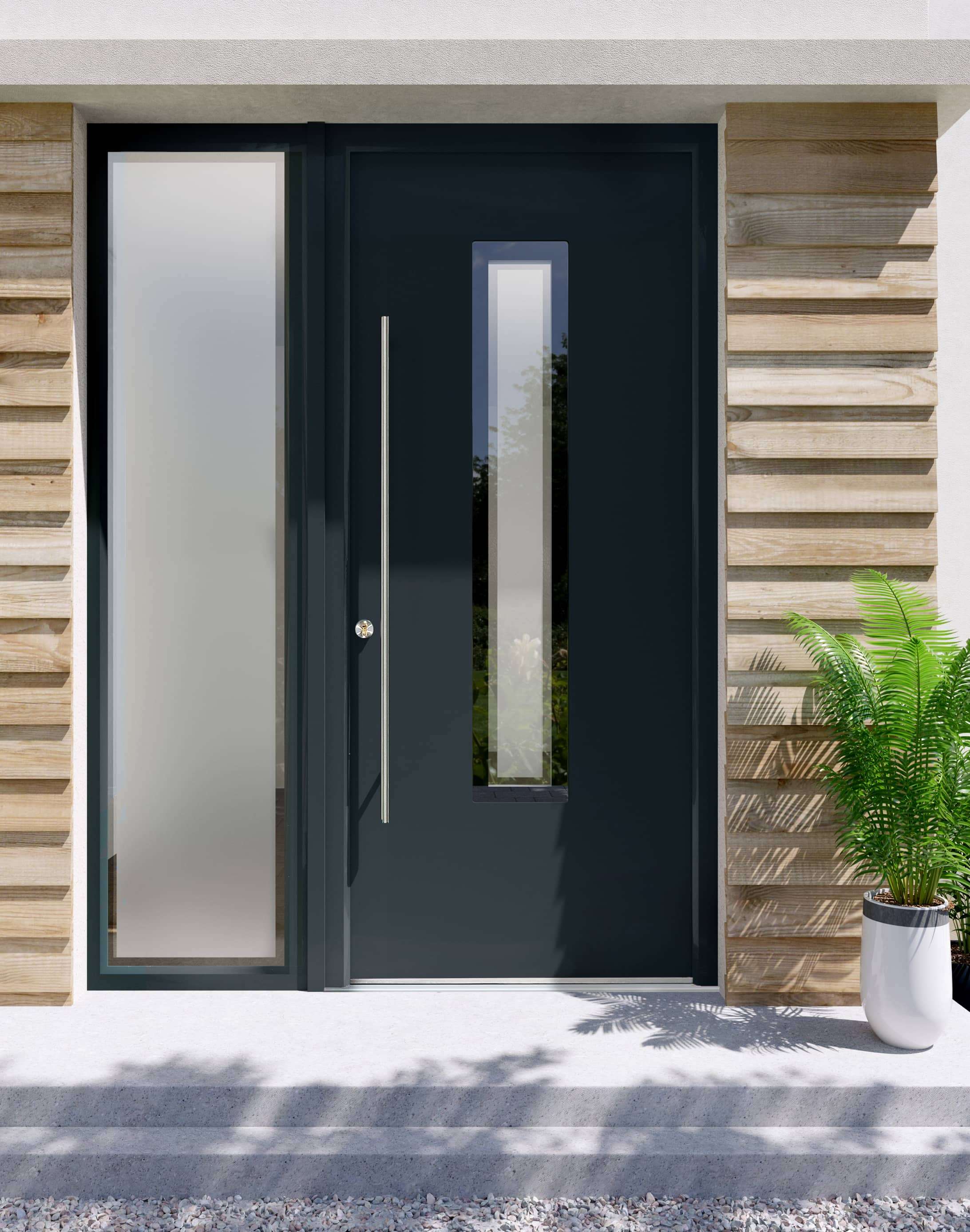
Yeah that’s some video for an entrance door, isn’t it? What they’ve done is use a splatter finish when moulding the fibreglass. Dead simple, but I think it works much much better. Yes when you actually touch the door and move it around, it’ll still feel fake, the door will be too light and the front it is plastic and no amount of splatter finish will eliminate that. But better I think to be pretending you’re something you’re not rather than claiming to be something you’re not.
U-value is < 0.8 installed, so it ticks the PH criterion. Door is 70 mm thick, so a little heftier than the Palladio door.
Let’s hope pricing is reasonable and there is a local Cork agent.
House build spend
It has been three months since the last house build spend update. This will be up to 1st January 2024:
- Spent: €243,207
- Committed to be spent soon: €14,374
- Current three month averaged spend rate: €7,293 per month
The three biggest ticket items in the past three months were: (i) Passive House certification fees (ii) Aliexpress on the Single’s Day heavily discounted sale, where I spent many thousands of euro buying all the lighting, dimmer switches, DC circuit breakers and lots of other odds and ends (iii) Final invoice for the Mechanical and Electrical design.
Last time I did an update on the house build spend I expected a build commencement in March. I would be surprised if we make April now, as the structural engineer is unlikely to get started before the end of January.
His fees will surely be the second largest item next time I do this end of March. I’m rather hoping that the largest fee will be the prepayment for doing the foundations, and the next time I do this house build spend update we will expect to break ground within weeks. Here’s hoping!
If I don’t draw down the mortgage by May, the offer will expire. I would expect that they will extend the offer, but I would prefer to not risk it especially when I have to front the costs of each stage in advance, and then recoup them from the bank after the work is signed off as complete. So if I fronted the cash, the mortgage offer expires before we can get the work signed off, and they then don’t renew the mortgage offer, then I am left in deep do doo .
Go to previous entry | Go to next entry | Go back to the archive index | Go back to the latest entries |